Shockproof mechanism of coal mining robot
A technology of robots and vibration sleeves, which is applied in the directions of slitting machinery, propulsion, earthwork drilling and mining, etc., can solve problems such as inoperability of robots, damage of robots, broken vibration sleeves, etc., so as to achieve smooth walking or operation when encountering obstacles, avoid failures and The effect of rollover and enhanced earthquake resistance
- Summary
- Abstract
- Description
- Claims
- Application Information
AI Technical Summary
Problems solved by technology
Method used
Image
Examples
Embodiment Construction
[0011] Such as figure 1 As shown, a shockproof mechanism for a coal digging robot includes a machine base 1 and a rotating cover 2 assembled above the machine base 1, and the front of the machine base is provided with a surrounding column 3, and the back is provided with a back support 4, in order to ensure that the robot works When it is damaged due to the falling of the ore from the mine shattering, this embodiment surrounds the column 3 or the back support 4 and is composed of four shock sleeves 5, and the upper, middle and lower sides of the shock sleeve 5 are provided with rotating drive wheels 6 , through four shock sleeves 5, it is not easy to break when the surrounding column 3 or back support 4 collides with the ore, and the shock sleeves 5 are reinforced on the upper, lower, left, and right sides of the machine base 1, so that the ore that is cracked in the mine is the force point when it falls It is concentrated in the middle of the shock sleeve 5, that is, the mach...
PUM
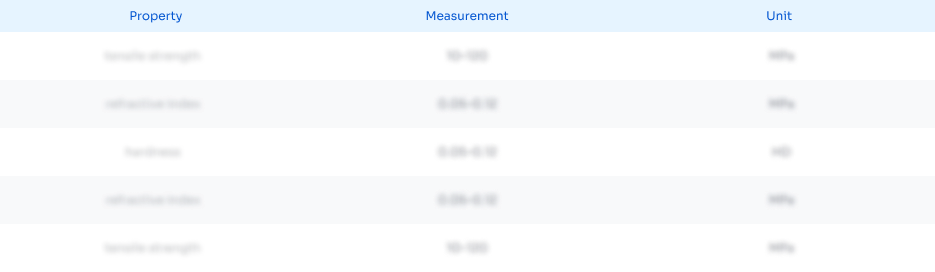
Abstract
Description
Claims
Application Information

- R&D
- Intellectual Property
- Life Sciences
- Materials
- Tech Scout
- Unparalleled Data Quality
- Higher Quality Content
- 60% Fewer Hallucinations
Browse by: Latest US Patents, China's latest patents, Technical Efficacy Thesaurus, Application Domain, Technology Topic, Popular Technical Reports.
© 2025 PatSnap. All rights reserved.Legal|Privacy policy|Modern Slavery Act Transparency Statement|Sitemap|About US| Contact US: help@patsnap.com