Flax mulberry fiber blend dyeing knitting yarn and manufacture method
A technology of mulberry fiber and flax fiber, applied in the field of knitting yarn
- Summary
- Abstract
- Description
- Claims
- Application Information
AI Technical Summary
Problems solved by technology
Method used
Image
Examples
Embodiment 1
[0028] (b) Roving semi-degumming: pickling, adding 2.8g / l compound acid and 2g / l penetrating agent, pickling temperature: 28°C, pickling time: 30 minutes;
[0029] (c), adding 1.5g / l of chlorinated chlorine for bleaching, the bleaching temperature is: 45°C, and the bleaching time is: 40 minutes;
[0030] Add 1g / L sodium sulfite for dechlorination, dechlorination temperature: 45°C, dechlorination time: 10 minutes;
[0031] Add hot water at 50°C for rinsing, the rinsing time is: 10 minutes;
[0032] (d), biological enzyme pretreatment before dyeing: add compound biological degumming enzyme 3.5 g / l and incubate at 50°C for 30 minutes, drain the liquid after treatment;
[0033] (e), dyeing: add dye with a weight ratio of 4% to the dyed yarn to be dyed; heat up to 60°C; cycle for 15 minutes; add salt: 20 g / l, sodium sulfate: 15 g / l; cycle for 15 minutes Minutes; add salt: 22g / l, sodium sulfate 15 g / l; cycle for 15 minutes; add salt: 20 g / l, sodium sulfate: 15 g / l; cycle for 25 mi...
Embodiment 2
[0038] (b) Roving semi-degumming: pickling, adding 3g / l compound acid and 2g / l penetrating agent, pickling temperature: 32°C, pickling time: 30 minutes;
[0039] (c), adding 0.7g / l of chlorinated chlorine to carry out bleaching, the bleaching temperature is: 45 ℃, and the bleaching time is: 42 minutes;
[0040] Add 1.5g / L sodium sulfite for dechlorination, dechlorination temperature: 47°C, dechlorination time: 12 minutes;
[0041] Add hot water at 55°C for rinsing, the rinsing time is: 10 minutes;
[0042] (d) Biological enzyme pretreatment before dyeing: add compound biological degumming enzyme 4 g / l, incubate at 55°C for 35 minutes, drain after treatment;
[0043] (e), dyeing: add dyes with a weight ratio of 5% of the dyed yarn to be dyed; heat up to 60°C; cycle for 17 minutes; add salt: 25 g / l, sodium sulfate: 15 g / l; cycle 12 Minutes; add salt: 20 g / l, sodium sulfate 15 g / l; cycle for 10 minutes; add salt: 20 g / l, sodium sulfate: 17 g / l; cycle for 20 minutes; add soda as...
Embodiment 3
[0048] (b) Roving semi-degumming: pickling, adding 3.5g / l compound acid and 2.5g / l penetrating agent, pickling temperature: 32°C, pickling time: 35 minutes;
[0049] (c), adding 2g / l of chlorinated chlorine to carry out bleaching, the bleaching temperature is: 50 ℃, and the bleaching time is: 45 minutes;
[0050] Add 1g / L sodium sulfite for dechlorination, dechlorination temperature: 45°C, dechlorination time: 10 minutes;
[0051] Add hot water at 55°C for rinsing, the rinsing time is: 10 minutes;
[0052] (d) Biological enzyme pretreatment before dyeing: add compound biological degumming enzyme 4.5 g / l, incubate at 60°C for 40 minutes, drain after treatment;
[0053] (e), dyeing: add dye with a weight ratio of 6% to the dyed yarn to be dyed; heat up to 60°C; cycle for 20 minutes; add salt: 25 g / l, sodium sulfate: 20 g / l; cycle 10 Minutes; add salt: 20 g / l, sodium sulfate 15 g / l; cycle for 15 minutes; add salt: 25 g / l, sodium sulfate: 20 g / l; cycle for 20 minutes; add soda ...
PUM
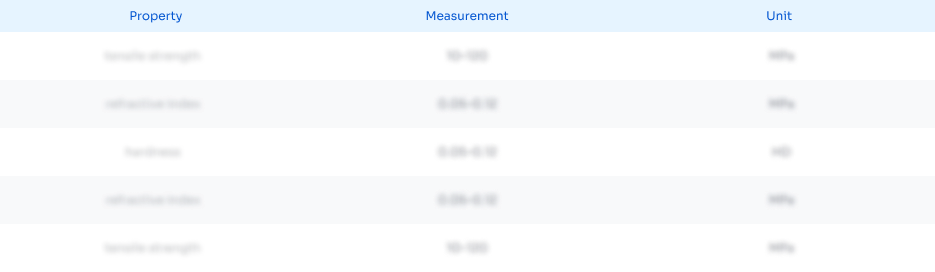
Abstract
Description
Claims
Application Information

- R&D Engineer
- R&D Manager
- IP Professional
- Industry Leading Data Capabilities
- Powerful AI technology
- Patent DNA Extraction
Browse by: Latest US Patents, China's latest patents, Technical Efficacy Thesaurus, Application Domain, Technology Topic, Popular Technical Reports.
© 2024 PatSnap. All rights reserved.Legal|Privacy policy|Modern Slavery Act Transparency Statement|Sitemap|About US| Contact US: help@patsnap.com