Robot steering engine with flexible characteristic
A robot and characteristic technology, applied in the field of robots, can solve the problems of troublesome installation and disassembly, and the rigidity of the elastic part cannot be adjusted, so as to reduce the space, realize the compliant drive, and ensure the work performance.
- Summary
- Abstract
- Description
- Claims
- Application Information
AI Technical Summary
Problems solved by technology
Method used
Image
Examples
Embodiment 1
[0042] Embodiment one, such as Figure 3-6 shown.
[0043] A cross-sectional view of a flexible gear 15 preloaded with a single-plate torsion spring. The flexible gear 15 is composed of a first hub 16, a first washer 17, a first screw 18, a first leaf torsion spring 19, a ring gear 20, a second Screw 21 forms.
[0044] The inner diameter of the ring gear 20 is the same as the outer diameter of the first hub 16, and the two are installed with a clearance fit. A threaded hole is opened on the ring gear 20 near the tooth root, and a threaded hole is also opened on the first wheel hub 16 near the output shaft. A first gasket 17 and a first leaf torsion spring 19 are installed between the inner surface of the first hub 16 and the first ring gear 20, wherein the first leaf torsion spring 19 is located below the first gasket 17; The gasket 17 and the first torsion spring 19 are positioned and installed with the first ring gear 20 and the first hub 16 respectively through the first s...
Embodiment 2
[0047] Embodiment two, such as Figure 7-10 shown.
[0048] A cross-sectional view of a flexible gear 15 preloaded with two torsion springs. The flexible gear 15 consists of a second hub 30, a third screw 31, a second washer 32, a second torsion spring 33, a fourth screw 34, a second The three-piece torsion spring 35 and the second ring gear 36 are formed.
[0049] The inner diameter of the second ring gear 36 is the same as the outer diameter of the second wheel hub 30, and the two are installed with a clearance fit.
[0050] The second ring gear 36 has a threaded hole and a through hole near the tooth root, and the second hub 30 has a boss structure near the output shaft. A second spacer 32 is installed between the second leaf type torsion spring 33 and the third leaf type torsion spring 35, and the three are placed below the ring gear 36, with threaded holes and through holes on it, through the third The screw 31 and the fourth screw 34 are positioned and installed.
[...
PUM
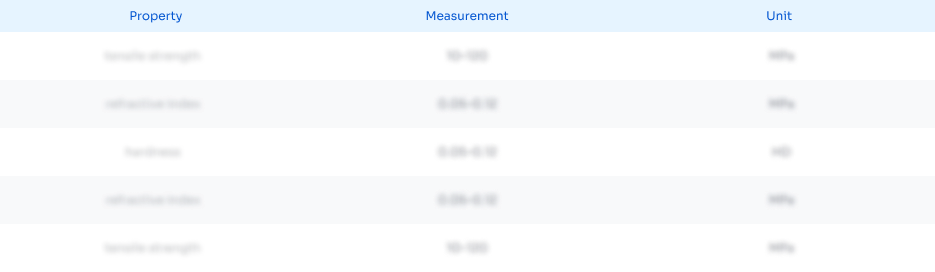
Abstract
Description
Claims
Application Information

- R&D Engineer
- R&D Manager
- IP Professional
- Industry Leading Data Capabilities
- Powerful AI technology
- Patent DNA Extraction
Browse by: Latest US Patents, China's latest patents, Technical Efficacy Thesaurus, Application Domain, Technology Topic, Popular Technical Reports.
© 2024 PatSnap. All rights reserved.Legal|Privacy policy|Modern Slavery Act Transparency Statement|Sitemap|About US| Contact US: help@patsnap.com