Preparation method of composite catalyst for hydrogenation of coal tar
A technology of composite catalyst and coal tar, applied in the field of coal chemical industry, can solve problems such as low recycling efficiency, and achieve the effects of convenient filling, good activity and high catalytic efficiency
- Summary
- Abstract
- Description
- Claims
- Application Information
AI Technical Summary
Problems solved by technology
Method used
Examples
Embodiment 1
[0014] At room temperature, 5.69g of nickel nitrate (Ni(NO 3 ) 2 ·6H 2 O) and 1.38g ammonium molybdate (NH 4 ) 6 Mo 7 o 24 4H 2 O) be made into solution, add the diammonium hydrogen phosphate (NH of 3.45g ) 2 HPO 4 ), and adjust the pH value to about 2-3 with concentrated nitric acid. Then 8.1 g of MCM-41 molecular sieves were added to the solution, impregnated for 12 h, dried at 120° C. for 5 h, and then calcined at 500° C. in air for 8 h to obtain an oxide precursor. The phosphide oxide precursor was prepared by temperature-programmed reduction in a U-shaped tube. The heating program was as follows: from room temperature to 120°C and kept for 1h, then raised to 400°C at a rate of 5°C / min, kept for 1h, then raised to 500°C at a rate of 1°C / min, kept for 3h. h 2 The flow rate was 150 mL / min. The temperature of the catalyst prepared by the temperature-programmed reduction method was lowered to room temperature, with O 2 O with a content of 0.5-1.0% (volume fraction...
Embodiment 2
[0017] At room temperature, 5.69g of nickel nitrate (Ni(NO 3 ) 2 ·6H 2 O) and 1.5g ammonium molybdate (NH 4 ) 6 Mo 7 o 24 4H 2 O) make solution, add 2.079 diammonium hydrogen phosphate (NH4) 2 HPO 4 ), and adjust the pH value to about 2-3 with concentrated nitric acid. Then, 6.09 g of γ-type molecular sieves were added into the solution, impregnated for 18 h, dried at 110° C. for 8 h, and then calcined at 700° C. in air for 6 h to obtain an oxide precursor. The phosphide oxide precursor was prepared by temperature-programmed reduction in a U-shaped tube. The heating program is as follows: from room temperature to 100°C and maintain for 2h, then increase the temperature at a rate of 3°C / min to 450°C, maintain for 1h, then increase the rate of temperature to 600°C at a rate of 1°C / min, and maintain for 3h. h 2 The flow rate was 120 mL / min. The temperature of the catalyst prepared by the temperature-programmed reduction method was lowered to room temperature, and the ...
Embodiment 3
[0020] At room temperature, 5.6g of nickel nitrate (Ni(NO 3 ) 2 ·6H 2 O) and 1.8g ammonium molybdate (NH 4 ) 6 Mo 7 o 24 4H 2 O) make solution, add 2.079 diammonium hydrogen phosphate (NH4) 2 HPO 4 ), and adjust the pH value to about 2-3 with concentrated nitric acid. Then 6.75g of mordenite was added into the solution, impregnated for 12h, dried at 130°C for 2h, and then calcined at 800°C in air for 4h to prepare the oxide precursor. The phosphide oxide precursors were prepared by temperature-programmed reduction in a fixed-bed reactor. The heating program was as follows: from room temperature to 120°C and kept for 1 h, then raised to 400°C at a rate of 4°C / min, kept for 1h, then raised to 650°C at a rate of 2°C / min, and kept for 3h. h 2 The flow rate was 100 mL / min. The temperature of the catalyst prepared by the temperature-programmed reduction method was lowered to room temperature, and pure NH 3 The nickel phosphide catalyst was passivated for 5h to obtain th...
PUM
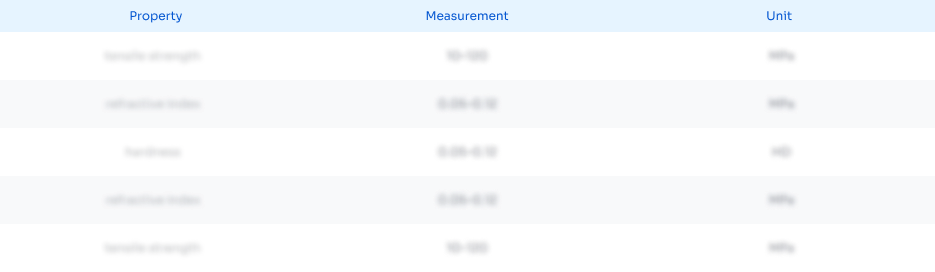
Abstract
Description
Claims
Application Information

- R&D Engineer
- R&D Manager
- IP Professional
- Industry Leading Data Capabilities
- Powerful AI technology
- Patent DNA Extraction
Browse by: Latest US Patents, China's latest patents, Technical Efficacy Thesaurus, Application Domain, Technology Topic, Popular Technical Reports.
© 2024 PatSnap. All rights reserved.Legal|Privacy policy|Modern Slavery Act Transparency Statement|Sitemap|About US| Contact US: help@patsnap.com