Full-load efficient backheating and fire coal drying system
A drying system, full-load technology, applied in the direction of drying gas layout, preheating, drying, etc., can solve the problems of coal pulverized coal outlet temperature not reaching the design value, poor boiler combustion, and increased extraction steam temperature.
- Summary
- Abstract
- Description
- Claims
- Application Information
AI Technical Summary
Problems solved by technology
Method used
Image
Examples
Embodiment Construction
[0030] Embodiments of the present invention will now be described in detail with reference to the accompanying drawings.
[0031] image 3 A schematic framework of a full-load high-efficiency heat recovery and coal-fired drying system according to the present invention is shown. like image 3 As shown, the full-load high-efficiency heat recovery and coal-fired drying system of the present invention mainly includes: cascaded multiple heaters 301-303, at least one high-load steam source 304, at least one low-load steam source 305, and coal-fired drying equipment 306. especially in image 3 Among them, the above-mentioned multiple heaters are successively condensed water heater 301, deaerator 302 and feed water heater 303, and correspondingly have three optional high-load steam sources 304, three optional low-load steam sources 305, and three optional low-load steam sources 305. A set of corresponding coal-fired drying equipment 306 is provided. Of course, the present inventio...
PUM
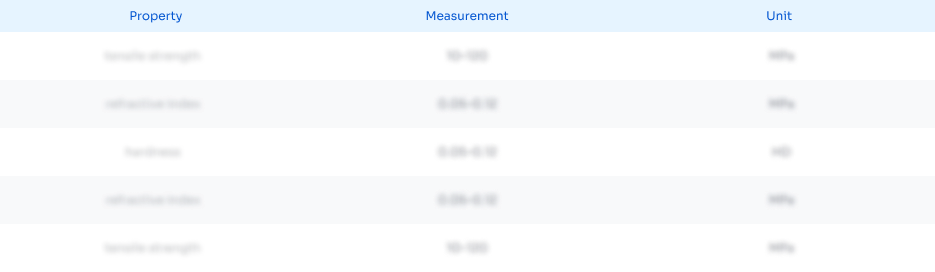
Abstract
Description
Claims
Application Information

- R&D Engineer
- R&D Manager
- IP Professional
- Industry Leading Data Capabilities
- Powerful AI technology
- Patent DNA Extraction
Browse by: Latest US Patents, China's latest patents, Technical Efficacy Thesaurus, Application Domain, Technology Topic, Popular Technical Reports.
© 2024 PatSnap. All rights reserved.Legal|Privacy policy|Modern Slavery Act Transparency Statement|Sitemap|About US| Contact US: help@patsnap.com