System for measuring nanometer micrometric displacement based on full-fiber frequency domain interference
A measurement system and micro-displacement technology, which is applied in the field of displacement sensors, can solve the problems that are difficult to meet the requirements of precision measurement and micro-electromechanical systems, and limit the wide application. Effect
- Summary
- Abstract
- Description
- Claims
- Application Information
AI Technical Summary
Problems solved by technology
Method used
Image
Examples
Embodiment Construction
[0015] figure 1 It is a schematic diagram of the structure of the all-fiber frequency-domain interference nano-micro-displacement measurement system of the present invention, as figure 1 As shown, the broadband light source 1 in the measurement system of the present invention is connected to the port I of the optical fiber circulator 2 through an optical fiber, the port II of the optical fiber circulator 2 is connected to the quartz fiber probe 3 through an optical fiber, and the port III of the optical fiber circulator 2 is connected to The spectrometer 4 is connected through an optical fiber, and the pigtails are connected through a flange or a welding method.
[0016] The spectral linewidth of broadband light source 1 is 10nm;
[0017] The optical fiber circulator 2 is a three-port circulator whose bandwidth includes the broadband light source 1. The light input from port I is output from port II, and the light input from port II is output from port III. Port I and port ...
PUM
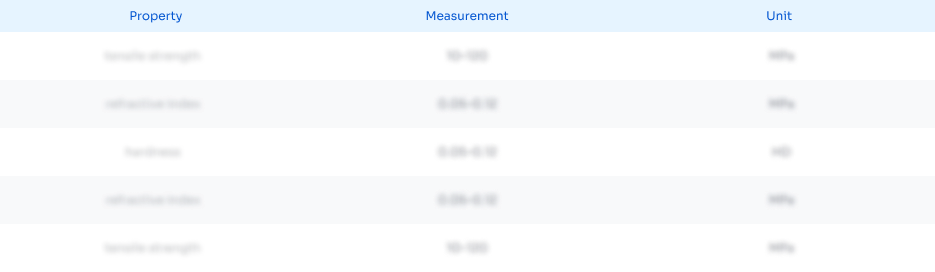
Abstract
Description
Claims
Application Information

- R&D
- Intellectual Property
- Life Sciences
- Materials
- Tech Scout
- Unparalleled Data Quality
- Higher Quality Content
- 60% Fewer Hallucinations
Browse by: Latest US Patents, China's latest patents, Technical Efficacy Thesaurus, Application Domain, Technology Topic, Popular Technical Reports.
© 2025 PatSnap. All rights reserved.Legal|Privacy policy|Modern Slavery Act Transparency Statement|Sitemap|About US| Contact US: help@patsnap.com