Methods for producing alkali cellulose and cellulose ether
一种碱纤维素、碱金属的技术,应用在生产纤维素醚领域,能够解决碱纤维素均匀性不足等问题,达到生产高的效果
- Summary
- Abstract
- Description
- Claims
- Application Information
AI Technical Summary
Problems solved by technology
Method used
Image
Examples
Embodiment 1
[0065] The pulp A sheet and the pulp B sheet were laminated and processed together with a cutter to produce mixed pulp chips AB of 10 mm2.
[0066]A screw conveyor type immersion tank including a screw conveyor with a screw diameter of 154 mm, a shaft diameter of 90 mm, a screw length of 1,500 mm, and a pitch of 100 mm was provided and the screw conveyor was rotated at 25 rpm. The mixed pulp chips AB were fed at a rate of 50 kg / hour into a screw conveying type immersion tank. Simultaneously, a 30° C. 49% by weight aqueous sodium hydroxide solution was fed into the tank at a rate of 1,700 L / hour from the sodium hydroxide inlet. An extruded plate type centrifugal dehydrator (which is a continuous centrifugal separator) with a 0.2 mm slit screen was installed at the end of the screw conveying type immersion tank. The centrifugal dehydrator deliquored the contact mixture between the mixed pulp chips and the aqueous sodium hydroxide solution, which had been discharged from the scr...
Embodiment 2
[0069] Pulp C and pulp D were used as raw materials. The ratio of the absorption rates of the aqueous sodium hydroxide solution of pulp D to pulp C (pulp D / pulp C) was 2.00.
[0070] Pulp C sheets and pulp D sheets were laminated and processed together with a cutter to produce mixed pulp chips CD of 10 mm2.
[0071] A tube having an inner diameter of 38 mm and a length of 10 m was provided and connected to a serpentine pump equipped with a hopper (Heishin Pump Works Co., Ltd., model NVL40PL) at the tube inlet. A 49% by weight aqueous sodium hydroxide solution at 40° C. was fed to the hopper at a rate of 1,100 L / h. At the same time, mixed pulp chips CD were fed at a rate of 50 kg / h. Connect the tube to the V-disc press at the end of the tube. The V-disk press continuously deliquors the contact mixture between the mixed pulp crumb and aqueous sodium hydroxide solution, which has been discharged from the pipe. The weight ratio of the alkali metal hydroxide in the resulting al...
Embodiment 3
[0074] Pulp E and pulp F were used as raw materials. The ratio of the absorption rates of the aqueous sodium hydroxide solution of pulp F to pulp E (pulp F / pulp E) was 4.00.
[0075] Pulp E sheets and pulp F sheets were laminated and processed together with a cutter to produce mixed pulp chips EF of 10 mm2.
[0076] A screw conveyor type immersion tank including a screw conveyor with a screw diameter of 154 mm, a shaft diameter of 90 mm, a screw length of 1,500 mm, and a pitch of 100 mm was provided and the screw conveyor was rotated at 30 rpm. The mixed pulp chips EF were fed at a rate of 50 kg / hour into a screw conveying type immersion tank. Simultaneously, a 49% by weight aqueous sodium hydroxide solution at 20° C. was fed into the tank at a rate of 1,700 L / hour from the sodium hydroxide inlet. An extruded plate type centrifugal dehydrator (which is a continuous centrifugal separator) with a 0.2 mm slit screen was installed at the end of the screw conveying type immersion...
PUM
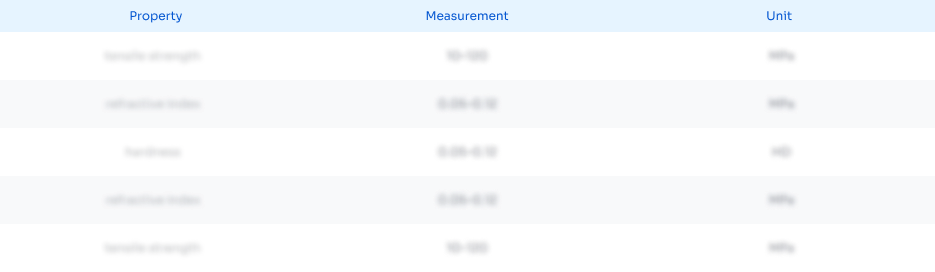
Abstract
Description
Claims
Application Information

- Generate Ideas
- Intellectual Property
- Life Sciences
- Materials
- Tech Scout
- Unparalleled Data Quality
- Higher Quality Content
- 60% Fewer Hallucinations
Browse by: Latest US Patents, China's latest patents, Technical Efficacy Thesaurus, Application Domain, Technology Topic, Popular Technical Reports.
© 2025 PatSnap. All rights reserved.Legal|Privacy policy|Modern Slavery Act Transparency Statement|Sitemap|About US| Contact US: help@patsnap.com