Long-stroke high-speed dual-drive nano positioning system
A nano-positioning, large-stroke technology, applied in electrical program control, digital control, etc., can solve the problems of being limited to micron level and the stroke can only reach tens of microns, and achieve the effect of improving response speed and positioning accuracy
- Summary
- Abstract
- Description
- Claims
- Application Information
AI Technical Summary
Problems solved by technology
Method used
Image
Examples
Embodiment Construction
[0019] The structural principle and working principle of the present invention will be further described in detail below in conjunction with the accompanying drawings.
[0020] figure 1 It is a basic schematic diagram of the present invention, such as figure 1 As shown, a large-stroke high-speed dual-drive nanopositioning system mainly includes a motion trajectory instruction system 101 , a main control computer 102 , a PMAC motion control board 103 , a servo motion control system 104 , a positioning platform, and a measurement control system 107 . The positioning platform includes a macro motion stage 105 and a micro motion stage 106 . First, the motion trajectory of the positioning platform (macro-motion stage 105 and micro-motion stage 106) is provided to the main control computer 102 by the motion trajectory instruction system 101, and the main control computer 102 sends the trajectory planning instruction to the PMAC motion control board 103 through the PEWIN interface ...
PUM
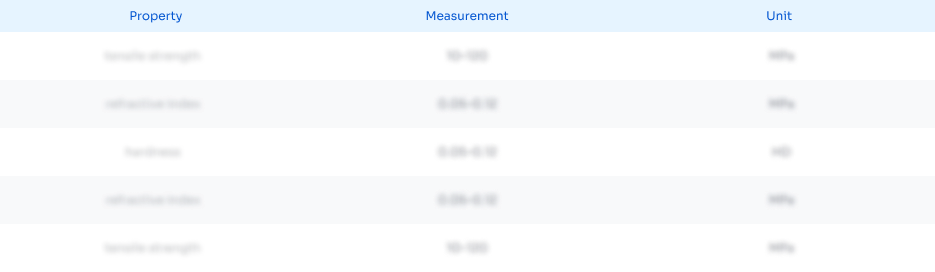
Abstract
Description
Claims
Application Information

- R&D
- Intellectual Property
- Life Sciences
- Materials
- Tech Scout
- Unparalleled Data Quality
- Higher Quality Content
- 60% Fewer Hallucinations
Browse by: Latest US Patents, China's latest patents, Technical Efficacy Thesaurus, Application Domain, Technology Topic, Popular Technical Reports.
© 2025 PatSnap. All rights reserved.Legal|Privacy policy|Modern Slavery Act Transparency Statement|Sitemap|About US| Contact US: help@patsnap.com