Light guide structure, backlight module and manufacturing method thereof
A manufacturing method and a backlight module technology are applied to the light guide plate structure, the backlight module and the manufacturing field thereof, and can solve the problems of low luminous efficiency, poor uniformity of white light emission, and difficult control of the uniformity of phosphor powder distribution, and achieve the effect of avoiding moisture.
- Summary
- Abstract
- Description
- Claims
- Application Information
AI Technical Summary
Problems solved by technology
Method used
Image
Examples
Embodiment Construction
[0055] The present invention will be described in detail below in conjunction with the accompanying drawings and specific embodiments, but not as a limitation of the present invention.
[0056] figure 1 It is a top view of the backlight module according to the first embodiment of the present invention. figure 2 It is a top view of the backlight module according to the second embodiment of the present invention. and image 3 for figure 1 and 2 Sectional view of the median line I-I. Figure 4 is a top view of a backlight module according to a third embodiment of the present invention, and Figure 5 for Figure 4 Sectional view of the median line II-II. Figure 6 is a bottom view of a backlight module according to a fourth embodiment of the present invention, and Figure 7 for Figure 6 Sectional view of the median line III-III.
[0057] refer to Figures 1 to 7 , the backlight module 10 includes a light guide plate structure 110 and at least one light source 120 .
...
PUM
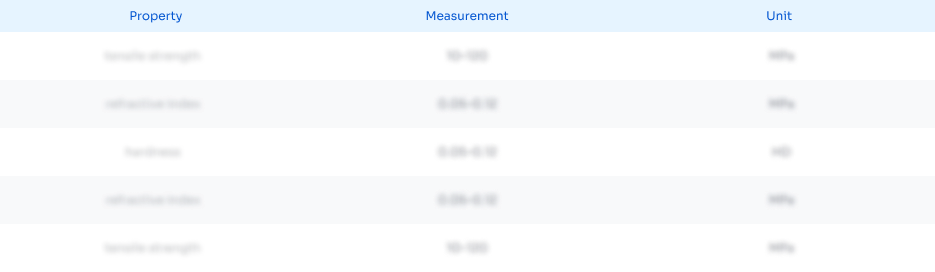
Abstract
Description
Claims
Application Information

- R&D Engineer
- R&D Manager
- IP Professional
- Industry Leading Data Capabilities
- Powerful AI technology
- Patent DNA Extraction
Browse by: Latest US Patents, China's latest patents, Technical Efficacy Thesaurus, Application Domain, Technology Topic, Popular Technical Reports.
© 2024 PatSnap. All rights reserved.Legal|Privacy policy|Modern Slavery Act Transparency Statement|Sitemap|About US| Contact US: help@patsnap.com