Speed regulation asynchronous magnetic coupler with adjustable radial air gap
A magnetic coupling and radial air gap technology, applied in electrical components, electromechanical devices, electromechanical transmission devices, etc., can solve the problems of limited application scope, high requirements on magnetic isolation cover materials, and difficult installation, and achieve overload protection. The effect of good performance and starting performance, expanding the application range and improving the utilization rate
- Summary
- Abstract
- Description
- Claims
- Application Information
AI Technical Summary
Problems solved by technology
Method used
Image
Examples
Embodiment 1
[0032] The working principle of embodiment 1: when the outer rotor rotates with the motor, the permanent magnet 5 embedded in the bottom groove of the movable card body 4 will generate an alternating magnetic field in the air gap whose size and direction change according to a certain law, according to According to Lenz's law, when the guide bar 11 cuts the magnetic force line, an induced current will be generated. This current interacts with the alternating magnetic field, so that the inner rotor receives an electromagnetic torque in the same direction as the alternating magnetic field, so that the inner rotor rotates. When the wrench 21 rotates any one of the four small bevel gears 17 on the circumference clockwise, the large bevel gear 18 in the disc body 14 rotates counterclockwise, and the plane thread 15 on the back side also rotates counterclockwise, thereby driving the movable card body 4 move radially toward the center at the same time, the length of the air gap between...
Embodiment 2
[0033] The working principle of embodiment 2: on the basis of embodiment 1, the guide bar 11 in the inner rotor assembly is replaced with the copper skin 23 wrapped on the inner solid rotor, when the wrench 21 turns clockwise the four Any one of the small bevel gears 17, the large bevel gear 18 in the disc body 14 rotates counterclockwise, and the plane thread 15 on its back side also rotates counterclockwise, driving the movable card body 4 to move radially toward the center of the disc body 14 at the same time. , the length of the air gap between the permanent magnet 5 and the outer copper skin 23 becomes smaller, the force of the air gap magnetic field becomes larger, and the output torque becomes larger; During any one, the large bevel gear 18 rotates clockwise, and the plane thread 15 on its back side also rotates clockwise, driving the movable card body 4 away from the center of the disc body 14 at the same time, the air gap length between the permanent magnet 5 and the o...
PUM
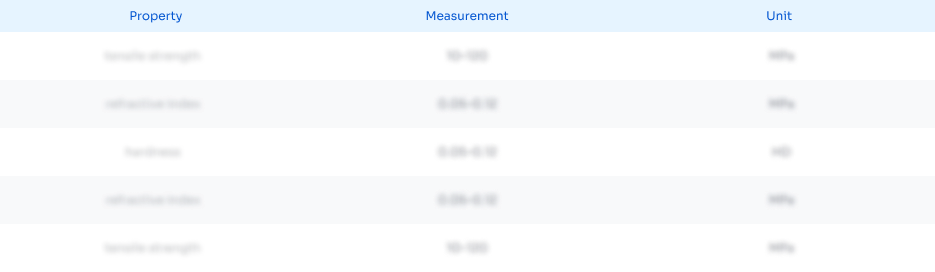
Abstract
Description
Claims
Application Information

- Generate Ideas
- Intellectual Property
- Life Sciences
- Materials
- Tech Scout
- Unparalleled Data Quality
- Higher Quality Content
- 60% Fewer Hallucinations
Browse by: Latest US Patents, China's latest patents, Technical Efficacy Thesaurus, Application Domain, Technology Topic, Popular Technical Reports.
© 2025 PatSnap. All rights reserved.Legal|Privacy policy|Modern Slavery Act Transparency Statement|Sitemap|About US| Contact US: help@patsnap.com