Clean process for using glycerin to synthesize epichlorohydrin
A technology of epichlorohydrin and glycerin, applied in phosphorus compounds, inorganic chemistry, non-metallic elements, etc., can solve the problems of difficult handling, large by-products, inconvenient production, etc., and achieve the effect of reducing costs and cleaning production
- Summary
- Abstract
- Description
- Claims
- Application Information
AI Technical Summary
Problems solved by technology
Method used
Examples
example 1
[0027] Example 1 : (Using lime as saponification alkali source, by-product phosphate fertilizer, continuous and stable operation)
[0028] 222kg / h (containing 33%HCl, 67%H 2 O) (from the airflow drying process of concentrated saponified wastewater and phosphoric acid reaction mixture) and 155kg / h of phosphorus oxychloride were continuously hydrolyzed at 60°C to produce 176kg / h of HCl gas and 201kg / h of dilute phosphoric acid aqueous solution by-product (including 48.8%H 3 PO 4 , 1.4%HCl and 49.8%H 2 O (mass ratio)). Heat and concentrate this dilute phosphoric acid aqueous solution at 120°C to concentrated phosphoric acid 122.5 kg / h (containing 80% H 3 PO 4 , 0.7%HCl and 19.3%H 2 O (mass ratio)), and produce 78.5㎏ / h dilute hydrochloric acid (containing 2.5%HCl, 97.5%H 2 O (mass ratio)).
[0029] POCl 3The HCl gas produced by hydrolysis is 176kg / h, which is pressed into the glycerin chlorination reactor with a reciprocating compressor, and 209kg / h industrial glycerin ...
example 2
[0032] Example 2 :((Using KOH as saponification alkali source, by-product phosphorus and potassium compound fertilizer, continuous and stable operation)
[0033] 158.6㎏ / h (containing 30.6% HCl, H 2 O 69.4%) and 124kg / h of phosphorus oxychloride were continuously hydrolyzed at 70°C to produce 132.8kg / h of HCl gas and 149.8kg / h of dilute phosphoric acid (containing 52.7%H 3 PO 4 , 2.2%HCl, 45.1%H 2 o). Heat and concentrate this dilute phosphoric acid aqueous solution at 120°C to obtain concentrated phosphoric acid 98 kg / h (containing 80% H 3 PO 4 , 20%H 2 O (mass ratio)).
[0034] The above POCl 3 132.8㎏ / h of HCl gas produced by hydrolysis is pressed into the glycerin chlorination reactor with a reciprocating compressor and 158.6㎏ / h of industrial glycerin (containing 96% glycerol) and 3kg / h of heavy components from the refining of epichlorohydrin Together, under the catalysis of 6kg / h adipic acid, chlorination reaction at 0.5MPa and 120℃ for 4h. The reaction mixture ...
PUM
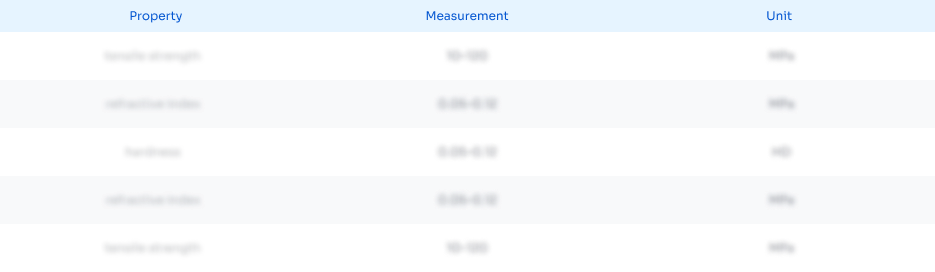
Abstract
Description
Claims
Application Information

- R&D Engineer
- R&D Manager
- IP Professional
- Industry Leading Data Capabilities
- Powerful AI technology
- Patent DNA Extraction
Browse by: Latest US Patents, China's latest patents, Technical Efficacy Thesaurus, Application Domain, Technology Topic, Popular Technical Reports.
© 2024 PatSnap. All rights reserved.Legal|Privacy policy|Modern Slavery Act Transparency Statement|Sitemap|About US| Contact US: help@patsnap.com