Two-degree-of-plane-freedom redundant drive parallel mechanism and machine tool with same
A degree of freedom, plane technology, used in milling machines, milling machine equipment, metal processing machinery parts, etc., can solve the problems of reduced mechanical efficiency, increased restraint reaction force of kinematic pairs, increased driving force, etc., to improve dynamic performance, stress Uniform, stiffness-increasing effect
- Summary
- Abstract
- Description
- Claims
- Application Information
AI Technical Summary
Problems solved by technology
Method used
Image
Examples
Embodiment Construction
[0015] The present invention will be described in detail below in conjunction with the accompanying drawings and embodiments.
[0016] Such as figure 1 As shown, the present invention includes a base 1 on which a first column 2 and a second column 3 are vertically spaced apart, and the tops of the first column 2 and the second column 3 are connected to the same beam 4 . Sliding guide rails are provided on opposite sides of the first column 2 and the second column 3 . The upper part of the first column 2 is provided with a first servo motor 5, the output end of the first servo motor 5 is connected to the first ball screw 6, and the lower end of the first ball screw 6 is vertically supported on the first screw support seat 7, The first screw support seat 7 is arranged on the first column 2 , and the first ball screw 6 is provided with a first slider 8 which can vertically move up and down along the guide rail on the first column 2 . The top of the second column 3 is provided w...
PUM
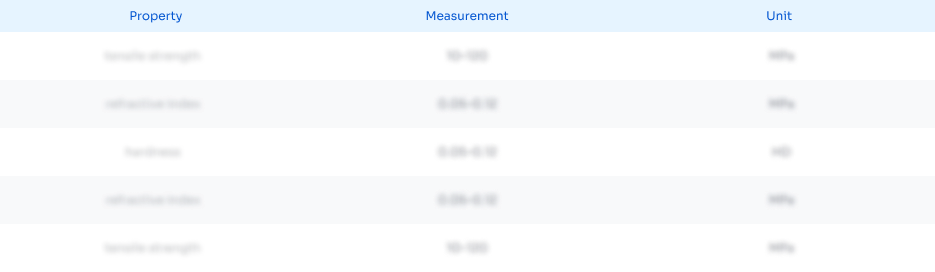
Abstract
Description
Claims
Application Information

- R&D
- Intellectual Property
- Life Sciences
- Materials
- Tech Scout
- Unparalleled Data Quality
- Higher Quality Content
- 60% Fewer Hallucinations
Browse by: Latest US Patents, China's latest patents, Technical Efficacy Thesaurus, Application Domain, Technology Topic, Popular Technical Reports.
© 2025 PatSnap. All rights reserved.Legal|Privacy policy|Modern Slavery Act Transparency Statement|Sitemap|About US| Contact US: help@patsnap.com