High-potential-difference potato starch-residue separation system
A technology for separation of potato starch and pulp residue, applied in the field of cassava starch processing, can solve the problems of high operating cost, complicated separation process of potato starch pulp and residue, and large land occupation, so as to reduce the use of equipment and improve the separation effect of pulp and residue. , the effect of good technical effect
- Summary
- Abstract
- Description
- Claims
- Application Information
AI Technical Summary
Problems solved by technology
Method used
Image
Examples
Embodiment
[0015] Example: The slurry is pumped into the primary vertical sieve at the highest point of the process. After screening, the slurry flows into the primary net sieve for screening, and the sieved slurry flows into the raw slurry tank and enters the next process. The primary vertical sieve The slag produced by the centrifugal force falls directly into the primary filter press, and the slag is further pressed dry, so that more starch emulsion is separated from the slag. Flow into the net sieve together, continue to sieve and separate, the slurry screened out by the net sieve flows into the slurry tank, and the whey enters the raw pulp tank and enters a process. The slag pressed out of the primary filter press falls into the mixing tank, and at the same time, it is stirred with clean water, and flows into the secondary vertical sieve through the pipeline through the high-level difference for centrifugation. , used for water distribution of the primary and secondary pulverizers, ...
PUM
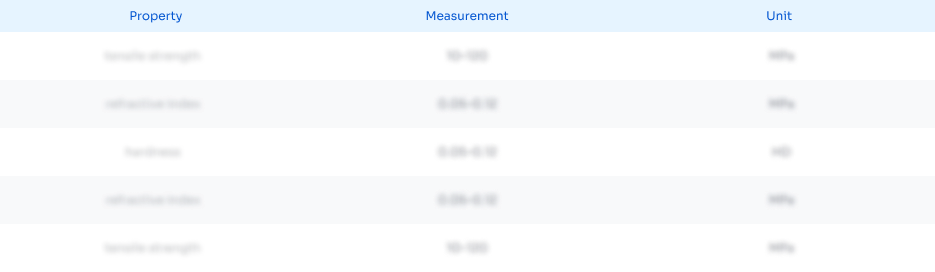
Abstract
Description
Claims
Application Information

- R&D
- Intellectual Property
- Life Sciences
- Materials
- Tech Scout
- Unparalleled Data Quality
- Higher Quality Content
- 60% Fewer Hallucinations
Browse by: Latest US Patents, China's latest patents, Technical Efficacy Thesaurus, Application Domain, Technology Topic, Popular Technical Reports.
© 2025 PatSnap. All rights reserved.Legal|Privacy policy|Modern Slavery Act Transparency Statement|Sitemap|About US| Contact US: help@patsnap.com