Machining process for guaranteeing precision of external circle of shaft sleeve
A processing method and precision technology, which is applied in the field of processing to ensure the accuracy of the outer circle of the shaft sleeve, can solve problems such as difficulty in ensuring the processing quality of the shaft sleeve, shape and position accuracy, and center distance difference, and affect the normal use of parts, so as to achieve easy use and promotion, The effect of ensuring machining accuracy
- Summary
- Abstract
- Description
- Claims
- Application Information
AI Technical Summary
Problems solved by technology
Method used
Examples
Embodiment Construction
[0009] A processing method for ensuring the accuracy of the outer circle of a shaft sleeve. The processing method includes the following steps: the processing method includes the following steps: cast steel blank→drawing a processing line on the blank→roughly milling each mounting surface, positioning surface and arc with a gantry milling machine →Use a vertical lathe to rough turn the front journal, inner hole and rear end inner hole →Casting defect inspection, flaw detection and welding repair →Stress relief annealing →Use a vertical lathe to semi-finish the front journal, finish turning inner hole and rear end inner Hole→mark machining and reference line on each surface→finish milling and drilling holes and screw holes on each mounting surface, positioning surface and surface with pentahedral machining center, and finish milling arc surface at the same time→mark each end surface hole, screw hole, shaft Neck oil hole position line→Drill end face holes, screw holes and oil hol...
PUM
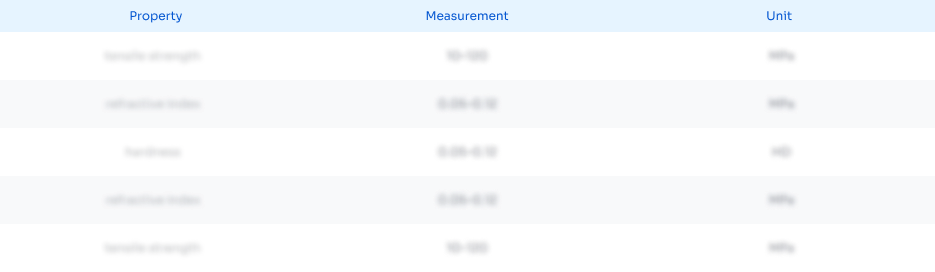
Abstract
Description
Claims
Application Information

- R&D Engineer
- R&D Manager
- IP Professional
- Industry Leading Data Capabilities
- Powerful AI technology
- Patent DNA Extraction
Browse by: Latest US Patents, China's latest patents, Technical Efficacy Thesaurus, Application Domain, Technology Topic, Popular Technical Reports.
© 2024 PatSnap. All rights reserved.Legal|Privacy policy|Modern Slavery Act Transparency Statement|Sitemap|About US| Contact US: help@patsnap.com