Automatic fillet welding device and automatic fillet welding method
A technology of automatic welding and fillet welding, which is used in welding equipment, auxiliary devices, welding equipment, etc., can solve the problems of the terminal that cannot be detected in the welding range, and cannot be specifically designated to be detected, and achieve the effect of reliable detection.
- Summary
- Abstract
- Description
- Claims
- Application Information
AI Technical Summary
Problems solved by technology
Method used
Image
Examples
Embodiment Construction
[0045] Embodiments of the present invention will be described below with reference to the drawings.
[0046] figure 1 The schematic structure of the fillet automatic welding apparatus in one Embodiment of this invention is shown, (a) is a side view, (b) is a top view.
[0047] Such as figure 1 As shown in (a), an automatic fillet weld welding device 1 (hereinafter simply referred to as a welding device) in this embodiment includes a trolley 3 and a welding torch 5 . The trolley 3 is configured to have two travel wheels 3a, 3b in the front and rear respectively, and utilizes a motor 3c (refer to figure 2 ) dynamics can be as figure 1 The travel direction X shown in (b) reciprocates. In addition, the four traveling wheels 3a, 3b may be independently driven by respective motors.
[0048] Such as figure 1 As shown in (a), a permanent magnet 3e is arranged on the bottom surface of the trolley 3, and the permanent magnet 3e is attached to the plate A (corresponding to the joi...
PUM
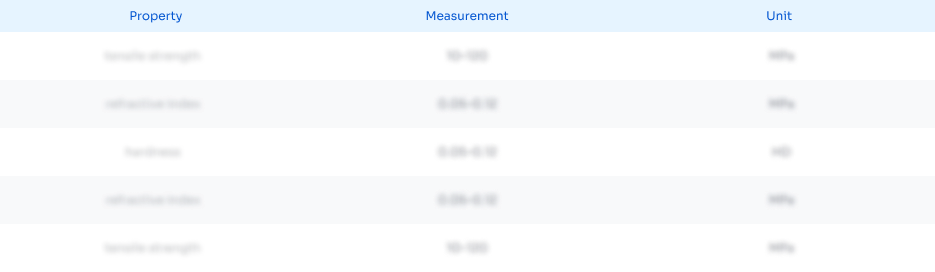
Abstract
Description
Claims
Application Information

- R&D Engineer
- R&D Manager
- IP Professional
- Industry Leading Data Capabilities
- Powerful AI technology
- Patent DNA Extraction
Browse by: Latest US Patents, China's latest patents, Technical Efficacy Thesaurus, Application Domain, Technology Topic, Popular Technical Reports.
© 2024 PatSnap. All rights reserved.Legal|Privacy policy|Modern Slavery Act Transparency Statement|Sitemap|About US| Contact US: help@patsnap.com