Beneficiation process for high-sulfur hematite
A hematite and high-sulfur technology, applied in flotation, magnetic separation, solid separation, etc., can solve the problems of no specific examples, and achieve the effects of reducing the amount of chemicals, reducing the cost of chemicals, and low sulfur content
- Summary
- Abstract
- Description
- Claims
- Application Information
AI Technical Summary
Problems solved by technology
Method used
Image
Examples
Embodiment 1
[0027] 1) Feed the high-sulfur hematite raw ore with a grade of 30.5% into the second-stage continuous ball mill, screen,
[0028] 2) The discharge ore with a particle size of -200 mesh and a content of more than 90% is fed with a weak magnetic field, and the tailings with a weak magnetic field are fed with a strong magnetic field.
[0029] 3) The weak magnetic concentrate and the strong magnetic concentrate were combined to obtain an iron grade of 45.30%, a sulfur content of 0.85%, and SiO 2 The rough concentrate with a content of 26.82% is put into the anion reverse flotation roughing together, and the desulfurization agent butyl xanthate 80-100g / t, the pH regulator NaOH 950-1150g / t, the inhibitor DF 450-800g / t , activator CaO 320-420g / t, collector 600-1000g / t,
[0030] 4) The concentrate obtained by anion reverse flotation roughing is fed into anion reverse flotation concentration, and collector 300-500g / t is added, and the tailings of anion reverse flotation concentration...
Embodiment 2
[0034] 1) Feed the high-sulfur hematite raw ore with a grade of 33% into the second-stage continuous ball mill, screen,
[0035] 2) The discharge ore with a particle size of -200 mesh and a content of more than 90% is fed with a weak magnetic field, and the tailings with a weak magnetic field are fed with a strong magnetic field.
[0036] 3) The weak magnetic concentrate and the strong magnetic concentrate were combined to obtain an iron grade of 47.30%, a sulfur content of 1.0%, and SiO 2 The rough concentrate with a content of 25.42% is fed into the anion reverse flotation roughing together, and the desulfurization agent butyl xanthate 80-100g / t, the pH regulator NaOH 950-1150g / t, the inhibitor DF 450-800g / t , activator CaO 320-420g / t, collector 600-1000g / t,
[0037]4) The concentrate obtained by anion reverse flotation roughing is fed into anion reverse flotation concentration, and collector 300-500g / t is added, and the tailings of anion reverse flotation concentration and...
PUM
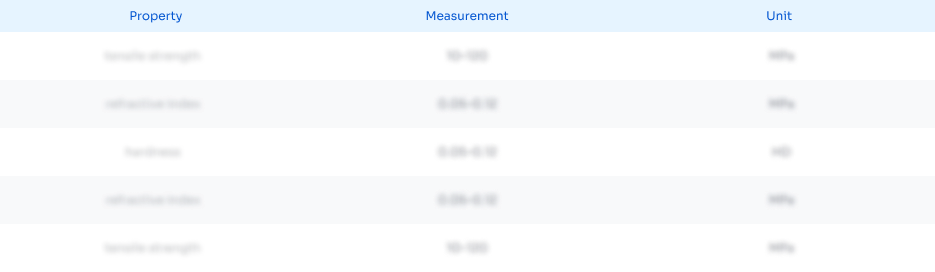
Abstract
Description
Claims
Application Information

- R&D
- Intellectual Property
- Life Sciences
- Materials
- Tech Scout
- Unparalleled Data Quality
- Higher Quality Content
- 60% Fewer Hallucinations
Browse by: Latest US Patents, China's latest patents, Technical Efficacy Thesaurus, Application Domain, Technology Topic, Popular Technical Reports.
© 2025 PatSnap. All rights reserved.Legal|Privacy policy|Modern Slavery Act Transparency Statement|Sitemap|About US| Contact US: help@patsnap.com