Method suitable for MEMS IMU repeated multiple calibrating
A technique of calibrating parameters and correction coefficients, which is applied in the testing/calibration of speed/acceleration/shock measuring equipment, measuring devices, instruments, etc., to avoid the risk of errors, reduce dependence, and improve reliability
- Summary
- Abstract
- Description
- Claims
- Application Information
AI Technical Summary
Problems solved by technology
Method used
Image
Examples
Embodiment Construction
[0029] The method applicable to multiple calibrations of MEMS IMUs is used for repeated and multiple calibrations of MEMS IMUs, and its purpose is to repeatedly calibrate MEMS IMUs reliably and efficiently. The characteristics of the present invention are: 1. The MEMS IMU can be repeatedly calibrated to calculate the correction coefficient of the calibration parameter without changing the software; 2. The MEMS IMU is controlled to upgrade the correction coefficient according to external instructions, and the external bus The interface of input and output data is common to the interface of MEMS IMU to realize its normal functions, which is simple and convenient, and is suitable for repeated calibration and coefficient upgrade of batch MEMS IMU products. 3. If there is any problem during the coefficient upgrade process of MEMSIMU, the upgrade will stop. The upgrade process can be restarted after the MEMS IMU is powered on and reset.
[0030] Such as figure 1 Shown, be applicab...
PUM
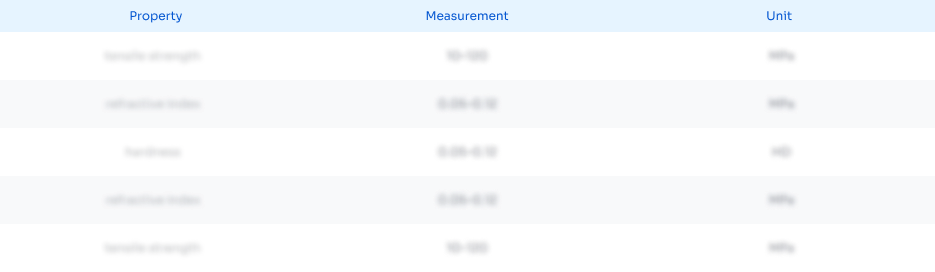
Abstract
Description
Claims
Application Information

- R&D
- Intellectual Property
- Life Sciences
- Materials
- Tech Scout
- Unparalleled Data Quality
- Higher Quality Content
- 60% Fewer Hallucinations
Browse by: Latest US Patents, China's latest patents, Technical Efficacy Thesaurus, Application Domain, Technology Topic, Popular Technical Reports.
© 2025 PatSnap. All rights reserved.Legal|Privacy policy|Modern Slavery Act Transparency Statement|Sitemap|About US| Contact US: help@patsnap.com