Dyeing method of white bamboo charcoal polyester fiber
A polyester fiber and dyeing method technology, which is applied in the field of fiber dyeing, can solve the problems of restricting the variety of finished products, not being able to meet the needs of market segments, and constraints, so as to increase the dyeing rate, color fastness and softness of hand, and optimize dyeing Process flow and parameters, effect of reducing impact
- Summary
- Abstract
- Description
- Claims
- Application Information
AI Technical Summary
Problems solved by technology
Method used
Examples
Embodiment 1
[0015] The white bamboo charcoal polyester fiber dyeing method described in this embodiment includes a desizing step, a dyeing step, an alkali weight reduction step, a reduction cleaning step and a drying step, and in the desizing step: prepare a 0.8% sodium carbonate solution; add Cleaning agent 209, the concentration is 0.5%; the bath ratio is 1:30, the desizing temperature is 80°C, after 30 minutes of desizing, take out the fibers and fabrics;
[0016] In the dyeing step: the fiber after desizing is put into the dyeing vat, and the proportioning of the dyeing solution is: reactive dyestuff is reactive blue B-BXF, mass fraction 3%; Yuanming powder 2%; Ammonium sulfate mass concentration is 0.5% ; The mass fraction of dispersant NNO is 0.1%; the pH value of the solution is 4.5; the temperature is 100°C;
[0017] In the alkali reduction step: put the dyed fiber into the alkali reduction tank, the alkali reduction solution formula, the mass concentration of sodium hydroxide is ...
Embodiment 2
[0020] The white bamboo charcoal polyester fiber dyeing method described in this embodiment, in the desizing step: prepare a sodium carbonate solution with a concentration of 0.8%; add detergent 207 with a concentration of 0.8%; the desizing temperature is 80°C, and after 40 minutes of desizing , take out the fiber and fabric; in the dyeing step: the reactive dyestuff is reactive red B-2BF, the mass fraction is 5%, the sodium sulfate is 3%, the ammonium sulfate mass concentration is 0.1%, the dispersant NNO mass fraction is 0.1%, the pH value 5.5, temperature 100°C; in the alkali reduction step: the mass concentration of sodium hydroxide is 5%, the accelerator is accelerator PM, the concentration is 0.1%, the treatment time is 30 minutes, and the temperature is 90°C; in the reduction cleaning step : The concentration of sodium carbonate is 0.2%, the concentration of detergent is 0.5%, the concentration of silane softener is 2.5%, the cleaning time is 10 minutes, and the tempera...
Embodiment 3
[0022] The white bamboo charcoal polyester fiber dyeing method described in this embodiment, in the desizing step: prepare a sodium carbonate solution with a concentration of 1%; add detergent 209 with a concentration of 1.5%; desizing temperature is 90 ° C, after 60 minutes of desizing , take out the fiber and fabric; in the dyeing step: the reactive dyestuff is reactive yellow B-6GLN, mass fraction 7%, sodium sulfate 5%, ammonium sulfate mass concentration is 0.3%, dispersant NNO mass fraction is 0.2%, pH value 6, the temperature is 100°C; in the alkali reduction step: the mass concentration of sodium hydroxide is 5%, the accelerator is the accelerator PM, the concentration is 0.1%, the treatment time is 30 minutes, and the temperature is 90°C; in the reduction cleaning step : The concentration of sodium carbonate is 0.5%, the concentration of detergent is 0.2%, the concentration of silane softener is 2.5%, the cleaning time is 10 minutes, and the temperature is 90°C. Others...
PUM
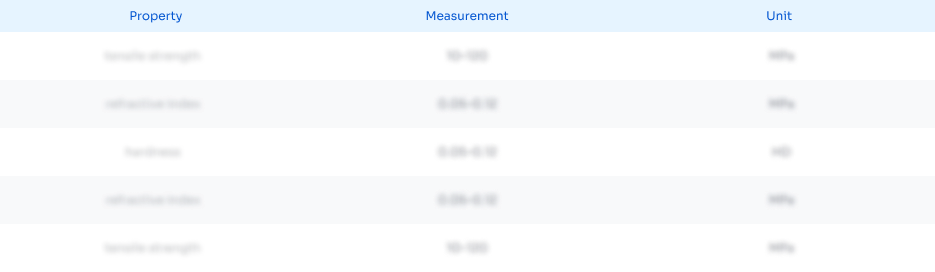
Abstract
Description
Claims
Application Information

- Generate Ideas
- Intellectual Property
- Life Sciences
- Materials
- Tech Scout
- Unparalleled Data Quality
- Higher Quality Content
- 60% Fewer Hallucinations
Browse by: Latest US Patents, China's latest patents, Technical Efficacy Thesaurus, Application Domain, Technology Topic, Popular Technical Reports.
© 2025 PatSnap. All rights reserved.Legal|Privacy policy|Modern Slavery Act Transparency Statement|Sitemap|About US| Contact US: help@patsnap.com