Self-adaptive biomimetic composite propeller blade
A bionic composite material and propeller technology, applied in the direction of rotating propellers, rotary propellers, etc., can solve the problems of complex and expensive pitch control mechanism, increase the overall manufacturing cost of ships, etc., achieve broad application prospects, avoid serious waste of main engine power, reduce The effect of manufacturing cost
- Summary
- Abstract
- Description
- Claims
- Application Information
AI Technical Summary
Problems solved by technology
Method used
Image
Examples
Embodiment Construction
[0017] The specific implementation manners of the present invention will be further described in detail below in conjunction with the accompanying drawings.
[0018] like figure 1 As shown, the blade body 100 is composed of the leading edge part 1 and the trailing edge part 2, the leading edge part 1 is arranged around the propeller reference shaft 200, the leading edge part 1 is provided with a rigid blade core 3, and the blade core 3 is covered with a flexible material Layer 4, the flexible material layer 4 is extended along the chord length direction to form the edge portion 2, and the side inclination distribution of the blade body 100 gradually increases from the blade root to the tip, so that the edge portion 2 is distributed behind the reference axis 200, and the flexible The material of the material layer 4 is carbon fiber or glass fiber composite material, and the blade core 3 is made of high-rigidity metal material, and various materials meet the strength requirement...
PUM
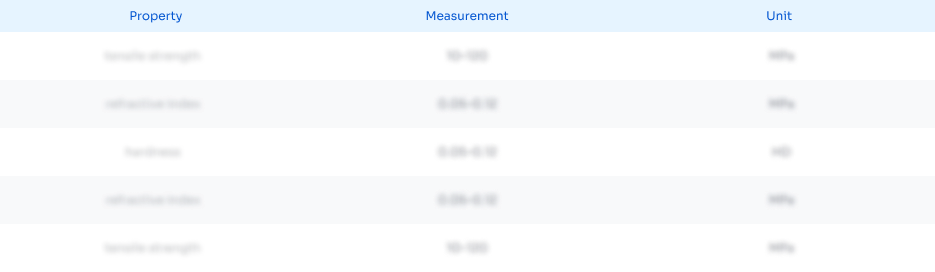
Abstract
Description
Claims
Application Information

- R&D
- Intellectual Property
- Life Sciences
- Materials
- Tech Scout
- Unparalleled Data Quality
- Higher Quality Content
- 60% Fewer Hallucinations
Browse by: Latest US Patents, China's latest patents, Technical Efficacy Thesaurus, Application Domain, Technology Topic, Popular Technical Reports.
© 2025 PatSnap. All rights reserved.Legal|Privacy policy|Modern Slavery Act Transparency Statement|Sitemap|About US| Contact US: help@patsnap.com