Step-by-step friction stir brazing method for thick aluminium plate and rigid dissimilar material
A dissimilar material, friction stir technology, applied in welding equipment, welding equipment, non-electric welding equipment, etc., can solve problems such as low joint strength, poor film removal and mixing, heating and pressure, and insufficient interface torsion, etc., to achieve high joint strength Effect
- Summary
- Abstract
- Description
- Claims
- Application Information
AI Technical Summary
Problems solved by technology
Method used
Image
Examples
Embodiment 1
[0062] Example 1: Step-by-step friction stir brazing technique between thick aluminum plate / stainless steel joints
[0063] As a feasibility test, in order to save test costs, the stainless steel plate (304) used is a thin plate with a thickness of 2mm and a size of 100mm×60mm. The thickness of the thick aluminum plate (1060) is 5mm; the thickness of the thin aluminum plate (1060) is 2mm; the size of the aluminum plate is also 100mm×60mm. The stirring tool is a needleless tool and a needle tool with a diameter of 20mm made of common 45 steel, respectively. The Zn foil is a commercially available 100 μm thick foil strip, and the width is also taken as 20 mm.
[0064] The welding process of the first layer is: as shown figure 1 (a) The method shown.
[0065] (1) Clamping method: The thin aluminum plate is clamped on the stainless steel plate (both plates are sanded and cleaned with alcohol), the brazing material Zn foil is placed between the two plates, and the stainless stee...
Embodiment 2
[0086] Example 2: Step-by-step friction stir brazing technology between thick aluminum plate / copper transition joints
[0087] Except that the 304 stainless steel plate was replaced by a copper plate (100mm×60mm×2mm in size), the materials, specifications and tools used were exactly the same as in Example 1.
[0088] The first step of welding process: the same method as in Example 1, a layer of thin aluminum plate is first brazed on the surface of the copper plate by using the needle-free friction stir brazing technology. Take a copper plate with a thickness of 2mm and a thin aluminum plate with a thickness of 2mm for the first step of brazing. The brazing material used is still Zn foil, and the welding speed is 150mm / min.
[0089] The second step of welding process: the same as the method in Example 1, the 5mm thick aluminum plate is welded on the thin aluminum plate of the thin aluminum / copper joint obtained in the first step with a needle tool, and the solder used is also Z...
PUM
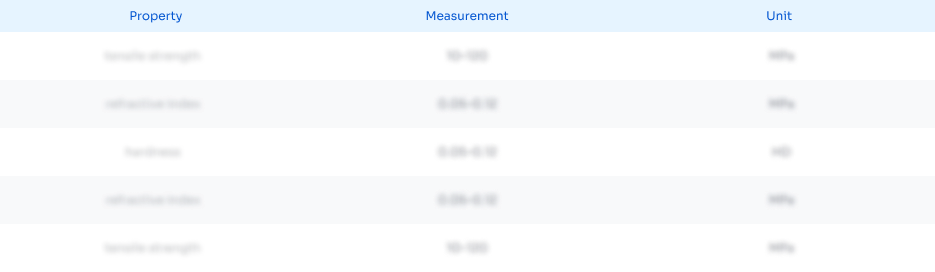
Abstract
Description
Claims
Application Information

- R&D
- Intellectual Property
- Life Sciences
- Materials
- Tech Scout
- Unparalleled Data Quality
- Higher Quality Content
- 60% Fewer Hallucinations
Browse by: Latest US Patents, China's latest patents, Technical Efficacy Thesaurus, Application Domain, Technology Topic, Popular Technical Reports.
© 2025 PatSnap. All rights reserved.Legal|Privacy policy|Modern Slavery Act Transparency Statement|Sitemap|About US| Contact US: help@patsnap.com