Fiber composite phosphoaluminate cement and slurry thereof and concrete preparation method
A technology of composite aluminophosphate and aluminophosphate cement, which is applied in the field of inorganic materials
- Summary
- Abstract
- Description
- Claims
- Application Information
AI Technical Summary
Problems solved by technology
Method used
Image
Examples
Embodiment 1
[0035] Embodiment 1, polyester fiber aluminophosphate composite cement (the parts by weight of its components are):
[0036] 52.5 grade aluminophosphate cement: 97.20;
[0037] Polyester fiber (fiber length: 6mm): 2.80.
Embodiment 2
[0038] Embodiment 2, glass fiber aluminophosphate composite cement (the parts by weight of its components are):
[0039] 52.5 grade aluminophosphate cement: 98.00;
[0040] Glass fiber (fiber length: 6mm): 2.00.
Embodiment 3
[0041] Embodiment 3, carbon fiber aluminophosphate composite cement (the parts by weight of its components are):
[0042] 52.5 grade aluminophosphate cement: 99.50;
[0043] Carbon fiber: 0.50.
[0044] In Examples 1 to 3, the designed ratio of fibers is uniformly added to the aluminophosphate cement being stirred and dry-mixed to form an aluminophosphate composite cement product. When in use, add a corresponding proportion of sand and water to the aluminophosphate composite cement product to mix and stir to form a mortar. Table 1 shows the main mechanical properties of fiber-aluminophosphate composite cement slurry under standard maintenance.
[0045] Table 1. Net fiber-aluminophosphate composite cement 1(Standard maintenance) main mechanical properties / MPa
[0046]
[0047] 1. Standard consistency of net pulp: drop depth of test needle: 30mm
PUM
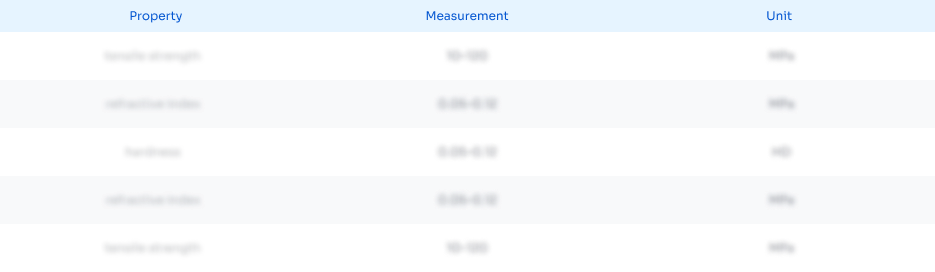
Abstract
Description
Claims
Application Information

- R&D
- Intellectual Property
- Life Sciences
- Materials
- Tech Scout
- Unparalleled Data Quality
- Higher Quality Content
- 60% Fewer Hallucinations
Browse by: Latest US Patents, China's latest patents, Technical Efficacy Thesaurus, Application Domain, Technology Topic, Popular Technical Reports.
© 2025 PatSnap. All rights reserved.Legal|Privacy policy|Modern Slavery Act Transparency Statement|Sitemap|About US| Contact US: help@patsnap.com