Sinking printing glaze and manufacturing method thereof
A technology of printing glaze and manufacturing method, which is applied in the field of ceramic glaze, which can solve the problems of lack of polishing, high processing cost, and additional equipment, etc., and achieve the effect of novel decorative effect, low cost, and rich colors
- Summary
- Abstract
- Description
- Claims
- Application Information
AI Technical Summary
Problems solved by technology
Method used
Image
Examples
Embodiment 1
[0035] Preparation of cryogenic solvents:
[0036] Ball mill red lead, talc, feldspar, titanium dioxide and quartz to pass through a 120-mesh sieve, sieve and mix, and calcinate at 1250°C for 45 minutes to obtain a low-temperature solvent, in which:
[0037] The weight percent of each component is:
[0038] PbO: 65.15%; MgO 0.51%; TiO 2 : 0.47%; Al 2 o 3 : 2.52%; SiO 2 : 29.39%; K 2 O: 1.57%; Na 2 O: 0.39%.
[0039] The weight percent of raw material is:
[0040] Red lead 70%, talc 1%, feldspar 5%, titanium dioxide? 0.5%, Quartz? 23.5%;
[0041] Preparation of sunken printing glaze:
[0042] Mix the above-mentioned low-temperature solvent, quartz, and alum pentoxide, add 30% water of the total weight of the mixture, ball mill it into a material with a fineness of 325 mesh sieve, dry, and pulverize to a fineness of 120 mesh sieve, Obtain sunken printing glaze;
[0043] The weight proportion of each component is:
[0044] Low temperature solvent: 40%, quartz: 40%, ...
Embodiment 2
[0048] Ball mill red lead, talc, feldspar, titanium dioxide and quartz until they pass through a 120-mesh sieve, mix them, and calcinate at 1240°C for 60 minutes to obtain a low-temperature solvent, among which:
[0049] The weight percent of each component is:
[0050] PbO: 68.35%; MgO 0.27%; TiO 2 : 0.18%; Al 2 o 3 : 1.48%; SiO 2 : 27.26%; K 2 O: 0.68%; Na 2 O: 1.78%.
[0051] The weight percent of raw material is:
[0052] Red lead 65.5%, talc 5%, feldspar 7%, titanium dioxide 1.5%, quartz 21%;
[0053] Preparation of sunken printing glaze:
[0054] Mix low-temperature solvent, quartz and alum pentoxide, add water with 40% of the total weight of the mixture, ball mill it into a material with a fineness of 325 mesh sieve, dry it, and crush it to a fineness of 120 mesh sieve to obtain a sunken print glaze;
[0055] The weight proportion of each component is:
[0056] Low temperature solvent 65%
[0057] Quartz 20%
[0059] Using m...
Embodiment 3
[0061] Preparation of cryogenic solvents:
[0062] Ball mill red lead, talc, feldspar, titanium dioxide and quartz to pass through a 120-mesh sieve, sieve and mix, and calcinate at 1245°C for 50 minutes to obtain a low-temperature solvent, in which:
[0063] The weight percent of each component is:
[0064] PbO: 62.18%; MgO 0.79%; TiO 2 : 0.89%; Al 2 o 3 : 2.94%; SiO 2 : 30.35%; K 2 O: 0.96%; Na 2 O: 1.89%.
[0065] The weight percent of raw material is:
[0066]Red lead 62%, talc 2%, feldspar 10%, titanium dioxide 1%, quartz 27%;
[0067] Preparation of sunken printing glaze:
[0068] Mix the above-mentioned low-temperature solvent, quartz, and alum pentoxide, add 35% water of the total weight of the mixture, ball mill it into a material with a fineness of 325 mesh sieve, dry, and pulverize to a fineness of 120 mesh sieve. Obtain sunken printing glaze;
[0069] The weight proportion of each component is:
[0070] Low temperature solvent: 50%, quartz: 32%, vanadium...
PUM
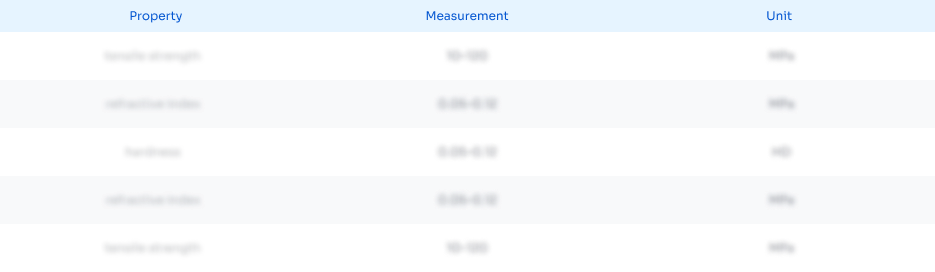
Abstract
Description
Claims
Application Information

- R&D Engineer
- R&D Manager
- IP Professional
- Industry Leading Data Capabilities
- Powerful AI technology
- Patent DNA Extraction
Browse by: Latest US Patents, China's latest patents, Technical Efficacy Thesaurus, Application Domain, Technology Topic, Popular Technical Reports.
© 2024 PatSnap. All rights reserved.Legal|Privacy policy|Modern Slavery Act Transparency Statement|Sitemap|About US| Contact US: help@patsnap.com