Processing process of large-diameter anti-static fiber glass epoxy plastic pipeline
An anti-static ring and processing technology, applied in the field of glass fiber reinforced plastics, can solve the problems of high defective rate, poor electrical conductivity, and easy generation of bubbles, etc., and achieve the effect of high resin content, smooth inner wall, and smooth appearance
- Summary
- Abstract
- Description
- Claims
- Application Information
AI Technical Summary
Problems solved by technology
Method used
Examples
Embodiment 1
[0017] Taking the manufacture of anti-static epoxy FRP pipes with a diameter of 1000mm, a pressure of 1.8Mpa and a length of 3000mm as an example, carbon fiber lining felt, high-strength carbon fiber, glass fiber and imported epoxy resin are used as raw materials, winding molding, computer control operation, steam Heating in stages, high temperature internal mold curing. The specific process is as follows:
[0018] 1. Material preparation: Prepare 28 rolls of high-strength glass fiber, about 16 kg per roll; 50 kg of epoxy resin; 45 kg of curing agent; 5 kg of accelerator; one roll of carbon fiber felt, 8 kg per roll (width is not limited); 2 high-strength carbon fibers, weighing 6kg; after the raw materials are prepared, pour epoxy resin, curing agent, and accelerator into the mixing tank for stirring. The stirring time is 10 minutes, and the speed is 200 rpm to obtain a well-stirred ring. Oxygen resin mixture 110kg, pour the stirred mixture into the bucket for subsequent use...
PUM
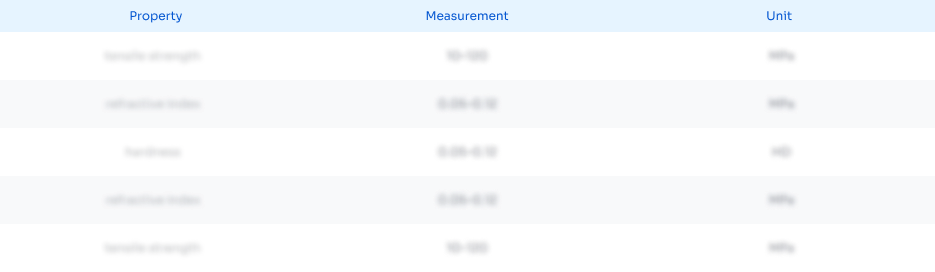
Abstract
Description
Claims
Application Information

- R&D
- Intellectual Property
- Life Sciences
- Materials
- Tech Scout
- Unparalleled Data Quality
- Higher Quality Content
- 60% Fewer Hallucinations
Browse by: Latest US Patents, China's latest patents, Technical Efficacy Thesaurus, Application Domain, Technology Topic, Popular Technical Reports.
© 2025 PatSnap. All rights reserved.Legal|Privacy policy|Modern Slavery Act Transparency Statement|Sitemap|About US| Contact US: help@patsnap.com