Device and method for realizing spatial three-dimensional variable curvature bending of pipe
A technology of variable curvature and pipe material, which is applied in the field of devices that realize three-dimensional variable curvature bending of pipe materials, can solve the problems of complex structure, high manufacturing cost, and bending defects of the bending device, and achieve simple structure, low manufacturing cost, and reduced wrinkling Effect
- Summary
- Abstract
- Description
- Claims
- Application Information
AI Technical Summary
Problems solved by technology
Method used
Image
Examples
Embodiment 1
[0040] Prepare multiple curved tubes with constant radius and straight segments alternating in the plane, such as figure 2 , Figure 5 As shown, the specific method is as follows: the pipe 1 enters the bending unit 2 through the guide unit 3 under the action of the rear push rod 4, and stops moving forward when the pipe 1 is fed to the first position that needs to be bent, and then uses the vertical motor 11 Drive the tube center on bending unit 2 according to figure 2 The trajectory moves from point o to r 1 Stop after the point, and now the rear push rod 4 promotes the pipe material 1 to move forward. When the end point of the first bending radius reaches the front end of the guide unit 3, the center of the pipe on the bending unit 2 is driven by the vertical motor 11 from r 1 The point returns to point o, and the pipe 1 moves forward all the time during this process, thus completing the first bending with a fixed radius. After the center of the pipe material on the be...
Embodiment 2
[0042] Prepare multiple curved pipes with constant radius and straight segments in space, such as image 3 , Image 6 As shown, the specific method is as follows: the pipe 1 enters the bending unit 2 through the guide unit 3 under the action of the rear push rod 4, and stops moving forward when the pipe 1 is fed to the first position that needs to be bent, and then is driven by a motor 11 Tube center on bending unit 2 according to image 3 The trajectory moves from point o to r 1 Point stops, and this moment, rear push rod 4 promotes pipe material 1 to move forward again. When the end point of the first bending radius reaches the front end of the guide unit 3, the center of the pipe on the bending unit 2 is driven by the vertical motor 11 from r 1 The point returns to point o, and the pipe 1 moves forward all the time during this process, thus completing the first bending with a fixed radius. After the center of the pipe on the bending unit 2 returns to point o, it stays f...
Embodiment 3
[0044] Prepare multiple curved tubes with varying radius and straight segments in the plane, such as figure 2 , Figure 7 As shown, the specific method is as follows: the pipe material 1 enters the bending unit 2 through the guide unit 3 under the action of the rear push rod 4, and when the pipe material 1 is fed to the first position that needs to be bent, the center of the pipe material on the bending unit 2 starts to be vertical Driven by the motor 11 according to figure 2 The trajectory moves from point o to r 1 point, the pipe 1 is always moving forward in this process. When the end point of the first bending radius reaches the front end of the guide unit 3, the center of the pipe on the bending unit 2 is driven by the vertical motor 11 from r 1 Point returns to point o, and pipe material 1 moves forward all the time during this process, thus completing the first bending with variable radius. The bending unit 2 stays for a while after returning to the o point, and t...
PUM
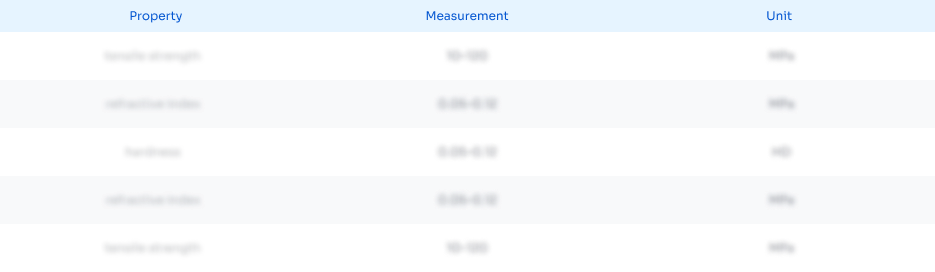
Abstract
Description
Claims
Application Information

- R&D
- Intellectual Property
- Life Sciences
- Materials
- Tech Scout
- Unparalleled Data Quality
- Higher Quality Content
- 60% Fewer Hallucinations
Browse by: Latest US Patents, China's latest patents, Technical Efficacy Thesaurus, Application Domain, Technology Topic, Popular Technical Reports.
© 2025 PatSnap. All rights reserved.Legal|Privacy policy|Modern Slavery Act Transparency Statement|Sitemap|About US| Contact US: help@patsnap.com