Six-component force sensor
A force sensor and six-component technology, applied in the field of mechanical parameter sensing devices, can solve the problem that force isotropy and moment isotropy cannot be realized at the same time, and achieve easy isotropy, simple mechanical analysis, and improved performance. Effect
- Summary
- Abstract
- Description
- Claims
- Application Information
AI Technical Summary
Problems solved by technology
Method used
Image
Examples
Embodiment 1
[0034] The sensor of the present invention comprises a main platform 2 and an auxiliary platform 3, and the casing 1 is arranged between the main platform 2 and the auxiliary platform 3, and the main platform 2 is provided with three spherical hinges 6 evenly spaced along the circumference, and each spherical hinge 6 is connected with a A support rod 4 in the horizontal direction and a support rod 5 in the vertical direction, the ball joint 6 and the support rod are all arranged in the shell 1; It is fixedly connected with the auxiliary platform 3.
[0035] The support rod is a pressure sensor, and the pressure sensor includes a horizontal tension pressure sensor 11 and a vertical tension pressure sensor 12 . The support rod is connected with the shell 1 and the auxiliary platform 3 through the Hooke hinge 7 . The main platform is provided with a platform connection hole 9 , and the casing 1 is provided with a casing connection hole 10 .
[0036] like Figure 9 As shown, di...
Embodiment 2
[0071] Such as Figure 12 As shown, the sensor includes a main platform 2 and two auxiliary platforms 3 on both sides, and each ball joint 6 is connected to four support rods, namely two support rods 4 in the horizontal direction and two support rods 5 in the vertical direction . The end of the support rod 4 in the horizontal direction is connected with the shell 1 through the Hooke 7 hinge, and the support rod 5 in the vertical direction is connected with the auxiliary platform 3 through the 7 Hooke hinge. Others are with embodiment 1.
Embodiment 3
[0073] Such as Figure 13 As shown, a force-sensitive element 13, such as a strain gauge, is set at an appropriate position on each support rod, combined with a processing circuit to form a force sensor and output six components of the measured force. Others are with embodiment 1.
PUM
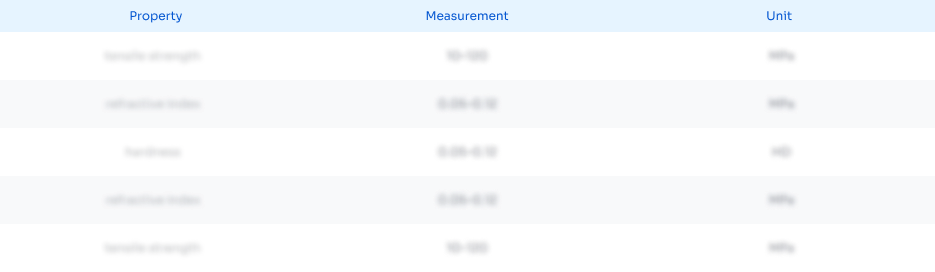
Abstract
Description
Claims
Application Information

- R&D
- Intellectual Property
- Life Sciences
- Materials
- Tech Scout
- Unparalleled Data Quality
- Higher Quality Content
- 60% Fewer Hallucinations
Browse by: Latest US Patents, China's latest patents, Technical Efficacy Thesaurus, Application Domain, Technology Topic, Popular Technical Reports.
© 2025 PatSnap. All rights reserved.Legal|Privacy policy|Modern Slavery Act Transparency Statement|Sitemap|About US| Contact US: help@patsnap.com