Method for preventing deformation of reinforcement steel plate welded on top flange of crane girder
A crane girder and flange technology, applied in the field of crane girder welding, can solve the problems of affecting the normal operation of the crane, the deformation of the reinforcing steel plate, and the unsatisfactory use, etc., and achieve the effect of simple structure, reducing deformation, and eliminating welding stress
- Summary
- Abstract
- Description
- Claims
- Application Information
AI Technical Summary
Problems solved by technology
Method used
Image
Examples
Embodiment Construction
[0013] The present invention will be further described in detail below in conjunction with the accompanying drawings and embodiments.
[0014] Embodiment of the present invention: when welding the reinforced steel plate 2 to the upper flange of the existing crane girder 1, a method of preventing the deformation of the reinforced steel plate welded on the upper flange of the crane girder of the present invention is used for welding, that is, first At least 3 through holes 3 are made at the position of the center line along the length direction on the reinforced steel plate 2, the through holes 3 on the reinforced steel plate 2 are preferably made into oval holes, and can also be made into round holes, the elliptical holes The width or diameter of the round hole can be determined according to the needs. Generally, it can be selected within the range of 6-30 mm. The length of the elliptical hole can be selected within the range of 10-60 mm. The distance L is controlled at 200-500...
PUM
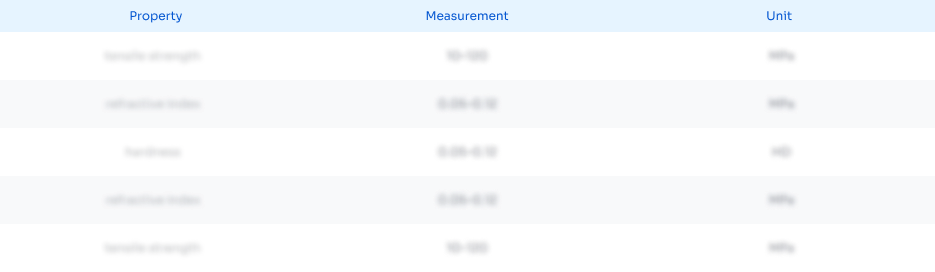
Abstract
Description
Claims
Application Information

- R&D
- Intellectual Property
- Life Sciences
- Materials
- Tech Scout
- Unparalleled Data Quality
- Higher Quality Content
- 60% Fewer Hallucinations
Browse by: Latest US Patents, China's latest patents, Technical Efficacy Thesaurus, Application Domain, Technology Topic, Popular Technical Reports.
© 2025 PatSnap. All rights reserved.Legal|Privacy policy|Modern Slavery Act Transparency Statement|Sitemap|About US| Contact US: help@patsnap.com