Manufacture method of non-aqueous printing ink wet underglaze colour self-sharpening polishing ceramic glazed tile
A manufacturing method and underglaze color technology, which is applied in the field of manufacturing non-aqueous ink wet underglaze color polished ceramic glazed tiles, can solve problems such as passivation, reduce power consumption and grinding head loss, improve the effect, and improve the production process simple effect
- Summary
- Abstract
- Description
- Claims
- Application Information
AI Technical Summary
Problems solved by technology
Method used
Image
Examples
Embodiment 1
[0028] Put the above-mentioned biscuit on the large-scale production conveyor line, first pour the bottom glaze, the glaze amount is 0.42kg / ㎡ (dry basis); then pour the opacified top glaze, the glaze amount is 0.42kg / ㎡ (dry basis); Inkjet printing according to the required pattern and color, and finally pour a layer of modified transparent glaze with 0.3% carboxyethyl cellulose, and the glaze amount is 0.45kg / ㎡ (dry basis). After the glaze layer is blotted dry, the glaze surface is flat and the pattern is evenly covered. Send it to a glaze firing kiln for firing. The maximum temperature of glaze firing is 1120°C, and the firing time is 60 minutes. The ceramic glazed tiles after glaze firing are transported to the attached figure 1 The polishing machine enters the brick platform 1, and every 25 pieces of the above-mentioned ceramic glazed tiles 2 add two pieces of unglazed ceramic bisque bricks 3 with the same thickness as the above-mentioned glazed tiles, 300mm×200mm, and the...
Embodiment 2
[0030] Put the above-mentioned biscuit on the large-scale production conveyor line, first pour the bottom glaze, the glaze amount is 0.45kg / ㎡ (dry basis); then pour the opacified top glaze, the glaze application amount is 0.40kg / ㎡ (dry basis); Ink-jet printing according to the required pattern and color, and finally pour a layer of modified transparent glaze with 0.35% carboxyethyl cellulose, the amount of glaze applied is 0.48kg / ㎡ (dry basis), and the glaze surface is smooth after the glaze layer is absorbed. The pattern is evenly covered. Send it to a glaze firing kiln for firing. The maximum glaze firing temperature is 1125°C, and the firing time is 58 minutes. The ceramic glazed tiles after glaze firing are transported to the attached figure 1The polishing machine enters the brick platform 1, and every 28 pieces of the above-mentioned ceramic glazed tiles 2 add two pieces of unglazed ceramic bisque bricks 3 with the same thickness as the above-mentioned glazed tiles, 300m...
Embodiment 3
[0032] Put the above-mentioned biscuit on the large-scale production conveyor line, first pour the bottom glaze, the glaze amount is 0.45kg / ㎡ (dry basis); then pour the opacified top glaze, the glaze application amount is 0.38kg / ㎡ (dry basis); Inkjet printing according to the required pattern and color, and finally pour a layer of modified transparent glaze with 0.35% carboxyethyl cellulose, and the glaze amount is 0.48kg / ㎡ (dry basis). After the glaze layer is blotted dry, the glaze surface is flat and the pattern is evenly covered. Send it to a glaze firing kiln for firing. The maximum glaze firing temperature is 1130°C, and the firing time is 55 minutes. The ceramic glazed tiles after glaze firing are transported to the attached figure 1 The polishing machine enters the brick platform 1, and every 30 pieces of the above-mentioned glazed ceramic tiles 2 add two pieces of unglazed ceramic bisque bricks 3 with the same thickness as the above-mentioned glazed tiles, 300mm×200m...
PUM
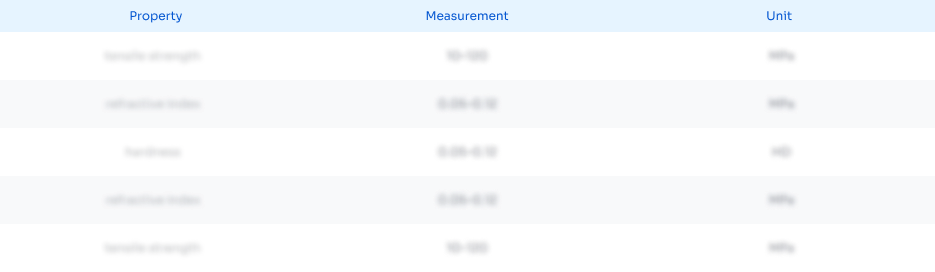
Abstract
Description
Claims
Application Information

- R&D
- Intellectual Property
- Life Sciences
- Materials
- Tech Scout
- Unparalleled Data Quality
- Higher Quality Content
- 60% Fewer Hallucinations
Browse by: Latest US Patents, China's latest patents, Technical Efficacy Thesaurus, Application Domain, Technology Topic, Popular Technical Reports.
© 2025 PatSnap. All rights reserved.Legal|Privacy policy|Modern Slavery Act Transparency Statement|Sitemap|About US| Contact US: help@patsnap.com