Annealing process for three-phase three-column amorphous alloy iron core
A three-phase three-column, amorphous iron core technology, applied in the field of transformers, can solve the problems of rising VA value and large impact on iron core performance, and achieve the effect of ensuring quality
- Summary
- Abstract
- Description
- Claims
- Application Information
AI Technical Summary
Problems solved by technology
Method used
Image
Examples
Embodiment Construction
[0017] The present invention will be further described below in conjunction with accompanying drawing and specific embodiment:
[0018] Such as figure 1 Shown: a three-phase three-column amorphous alloy core annealing process, including the following steps:
[0019] 1) Shape the sheared amorphous strips separately: a large frame core 2 and two small frame cores 1;
[0020] 2) Assemble the large frame core 2 and the small frame core 1 into a three-phase three-column amorphous core;
[0021] 3) Wrap the conductor row 3 with the corresponding number of turns on the above-mentioned three-phase three-column amorphous core, connect the conductor row 3, and heat-treat the three-phase three-column core as a whole;
[0022] 4) The heat-treated three-phase three-column amorphous core is finally treated to fix its performance, and then coated with epoxy resin to complete the entire annealing process.
PUM
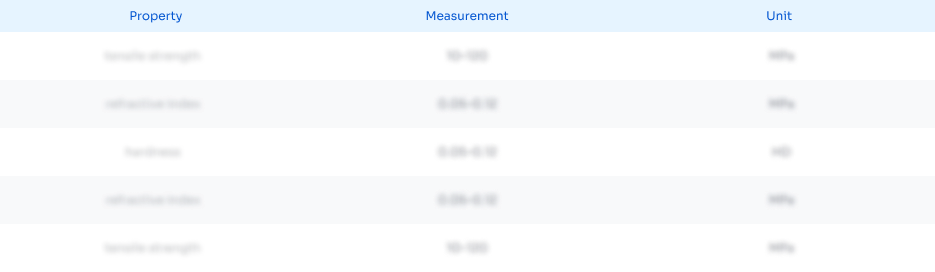
Abstract
Description
Claims
Application Information

- R&D Engineer
- R&D Manager
- IP Professional
- Industry Leading Data Capabilities
- Powerful AI technology
- Patent DNA Extraction
Browse by: Latest US Patents, China's latest patents, Technical Efficacy Thesaurus, Application Domain, Technology Topic, Popular Technical Reports.
© 2024 PatSnap. All rights reserved.Legal|Privacy policy|Modern Slavery Act Transparency Statement|Sitemap|About US| Contact US: help@patsnap.com