Method for reducing converter hot metal single consumption
A technology of molten iron and unit consumption, which is applied in the manufacture of converters, etc., can solve the problem of increasing scrap steel, and achieve the effects of reducing the unit consumption of molten iron, increasing economic benefits, and reducing production costs
- Summary
- Abstract
- Description
- Claims
- Application Information
AI Technical Summary
Problems solved by technology
Method used
Examples
Embodiment 1
[0028] Adopt 260t converter.
[0029] The actual weight of Si in molten iron [Si] is 0.45%. The actual temperature of molten iron entering the desulfurization station is T = 1380°C, which meets the standard conditions of molten iron. Just add 50t of scrap steel to the molten iron at one time.
Embodiment 2
[0031] Adopt 260t converter.
[0032] [Si] in molten iron = 0.3%, the actual temperature T of molten iron entering the desulfurization station is 1350°C, the measures of combining silicon and carbon are adopted, the silicon content of molten iron is adjusted first, and then coke is added for temperature compensation, and the molten iron is mixed to standard conditions.
[0033] Silicon mix: Compared with the minimum limit of standard conditions, [Si] in molten iron is 0.1% less, adding 1.35kg of ferrosilicon per ton of molten iron can increase the proportion of [Si] 0.1% in molten iron, so add it to the molten iron at one time 350kg of ferrosilicon containing 67% Si.
[0034] Carbon distribution: according to the coke addition formula:
[0035] W=(1380-T)×w=(1380-1350)×40=1200kg, so add 1200kg of coke containing 90% C to the molten iron.
[0036] Among them: 960kg of coke is added in the first batch when oxygen blowing starts, and the remaining 240kg of coke is added before...
Embodiment 3
[0039] Adopt 260t converter.
[0040] [Si] in molten iron is 0.27%, and the actual temperature T of molten iron entering the desulfurization station is 1300°C. First adjust the silicon content of molten iron, and then add coke for temperature compensation.
PUM
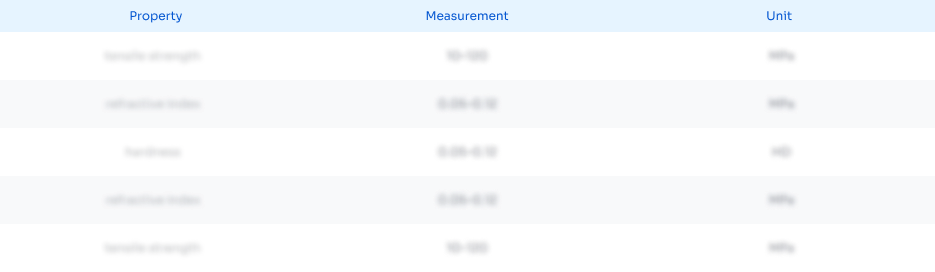
Abstract
Description
Claims
Application Information

- R&D
- Intellectual Property
- Life Sciences
- Materials
- Tech Scout
- Unparalleled Data Quality
- Higher Quality Content
- 60% Fewer Hallucinations
Browse by: Latest US Patents, China's latest patents, Technical Efficacy Thesaurus, Application Domain, Technology Topic, Popular Technical Reports.
© 2025 PatSnap. All rights reserved.Legal|Privacy policy|Modern Slavery Act Transparency Statement|Sitemap|About US| Contact US: help@patsnap.com