Polyurethane surface layer resin for shoe lining leather and preparation method thereof
The technology of surface layer resin and polyurethane is applied in the field of polyurethane surface layer resin for shoe lining and its preparation, which can solve the problems of poor synthetic leather, poor air permeability of lining, uncomfortable feet and the like, and achieve good economic benefits and social benefits. Benefit, good resin stability, avoid the effect of filler settling
- Summary
- Abstract
- Description
- Claims
- Application Information
AI Technical Summary
Problems solved by technology
Method used
Examples
Embodiment 1
[0016] Mix 20kg of polyester polyol, 1.9kg of butanediol and 21kg of DMF, stir evenly, then add 8.1kg of MDI, control the temperature at 70°C, and react until the viscosity is 1.0×10 6 -1.5×10 6 Between cps (25°C), add 49kg DMF, stir and react for 1 hour to obtain PU; mix 50kg PU, 5kg urea and 20kg DMF, stir and mix at room temperature at 3000r / min to obtain polyurethane surface layer resin for shoe lining pulp, wherein the polyester polyol is a copolymer of adipic acid and butanediol with a molecular weight of 2000.
[0017] The shoe lining is impregnated or coated on the base material with polyurethane surface layer resin slurry, and solidified in a water bath. DMF has good hydrophilicity and is quickly replaced by water, so that it can be quickly dissolved in water, so that the leather PU During the solidification process, countless small holes are left. At the same time, urea will also decompose under high temperature, forming countless pinholes in the PU film, which enh...
Embodiment 2
[0019] Take 40kg of polyester polyol, 3.8kg of butanediol and 50kg of DMF, mix well, then add 16.2kg of MDI, and react until the viscosity is 1.0×10 at 70°C 6 -1.5×10 6 cps (25°C), add 90kg DMF, stir and react for 1 hour to obtain PU; mix 100kg PU, 30kg urea and 50kg DMF, stir and mix at room temperature at 3000r / min to obtain polyurethane surface layer resin for shoe lining. Wherein, the polyester polyol is a copolymer of adipic acid and butanediol with a molecular weight of 2000.
[0020] The shoe lining is impregnated or coated with polyurethane surface layer resin slurry on the base material, and solidified in a water bath. DMF has good hydrophilicity and is quickly replaced by water and dissolved in water. During the solidification process of leather PU At the same time, urea also decomposes at high temperature, forming countless pinholes in the PU film, which enhances the air permeability of the original PU leather, and has the characteristics of good air permeability ...
Embodiment 3
[0022] Take 40kg of polyester polyol, 3.8kg of butanediol and 40kg of DMF, mix well, add 16.2kg of MDI, and react until the viscosity is 1.0×10 at 70°C 6 -1.5×10 6 cps / 25°C, add 100kg DMF, stir and react for 1 hour to obtain PU; mix 100kg PU, 13kg urea and 30kg DMF, and stir and mix at room temperature at 3000r / min to obtain polyurethane surface layer resin for shoe lining, wherein, Polyester polyol is a copolymer of adipic acid and butanediol with a molecular weight of 2000.
[0023] The shoe lining is impregnated or coated with polyurethane surface layer resin slurry on the base material, and solidified in a water bath. DMF has good hydrophilicity and is quickly replaced by water and dissolved in water. During the solidification process of leather PU At the same time, urea will also decompose at high temperature, forming countless pinholes in the PU film, which enhances the air permeability of the original PU leather, and has the characteristics of good air permeability an...
PUM
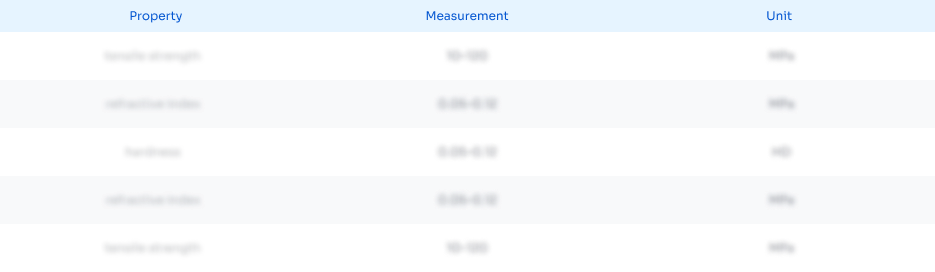
Abstract
Description
Claims
Application Information

- R&D Engineer
- R&D Manager
- IP Professional
- Industry Leading Data Capabilities
- Powerful AI technology
- Patent DNA Extraction
Browse by: Latest US Patents, China's latest patents, Technical Efficacy Thesaurus, Application Domain, Technology Topic, Popular Technical Reports.
© 2024 PatSnap. All rights reserved.Legal|Privacy policy|Modern Slavery Act Transparency Statement|Sitemap|About US| Contact US: help@patsnap.com