Real-time strain measurement apparatus for stamping and forming and test method thereof
A technology of strain measurement and stamping forming, which is applied in the field of real-time strain measurement devices, can solve the problems of non-contact testing methods, embedding sensors, and difficulty in testing, etc., to overcome real-time working condition testing, reduce stamping defects, low cost effect
- Summary
- Abstract
- Description
- Claims
- Application Information
AI Technical Summary
Problems solved by technology
Method used
Image
Examples
Embodiment 1
[0018] like figure 1 As shown, the real-time strain measurement device for stamping includes static strain gauge 6, wire 5, strain gauges 4-I, 4-II, 4-III, 4-IV, 4-V and dies, strain gauges 4-I, 4-Ⅱ, 4-Ⅲ, 4-Ⅳ, 4-Ⅴ are fixed on the corresponding test points of the plate 3, and the strain gauges 4-Ⅰ, 4-Ⅱ, 4-Ⅲ, 4-Ⅳ, 4-Ⅴ pass through the wire 5 Connected with the static strain gauge 6, the mold includes a die 1 and a die 2. The position corresponding to the test point of the die 2 is provided with a groove 7 for placing a strain gauge, and the groove 7 is on the front and rear symmetry lines of the die. The strain gauges are placed in the groove 7. The static strain gauge adopts the 1 / 4 bridge method. The strain gauges of all test points are connected to the AB bridge arm of the static strain gauge through wires, and the strain gauges of all test points share a compensation plate connected to the common compensation bridge arm of the static strain gauge.
Embodiment 2
[0020] A real-time strain measurement method for stamping, comprising the following steps:
[0021] (1) Equipped with a real-time strain measurement device for stamping: a mold consisting of static strain gauge 6, wire 5, strain gauges 4-I, 4-II, 4-III, 4-IV, etc., die 1 and die 2, Static strain gauge is 1 / 4 bridge method;
[0022] (2) According to the deformation characteristics of the workpiece, such as figure 2 As shown, in different deformation parts of the workpiece and parts with different strain characteristics, the two sides of the bending angle formed by stretch bending: w1 and w2, and several positions are determined on the surface (M surface) in contact with the die. Test points, paste the strain gauges 4-Ⅰ, 4-Ⅱ, 4-Ⅲ, 4-Ⅳ, 4-Ⅴ on the corresponding test points respectively;
[0023] (3) Process the groove 7 at the position corresponding to the test point determined in step (2) on the die, the position is as follows image 3 As shown, the strain gauge pasted on th...
Embodiment 3
[0026] figure 1 In this embodiment, the present embodiment is used to measure the stress and strain of a blank (workpiece) 3 in real time during the stamping process of a U-shaped piece by a stamping die. In this example, if Figure 4 As shown, five key points (test points) are taken in total on the flange edge of the U-shaped piece, one side close to the bending angle, the straightened wall of the U-shaped piece, and the bottom of the specimen (workpiece); these parts are U-shaped During the forming process of the molded part, the most severe or close to the most severe part of the mold force ensures that the strain is within the applicable range of the strain gauge. In order to ensure that the strain gauge 4 and the wire 5 are not affected by the mold during the stamping process, a groove 7 with a certain width and depth is processed on the position corresponding to the key point of the die 2, and the strain gauge is placed on the groove 7. out of groove 7. The static str...
PUM
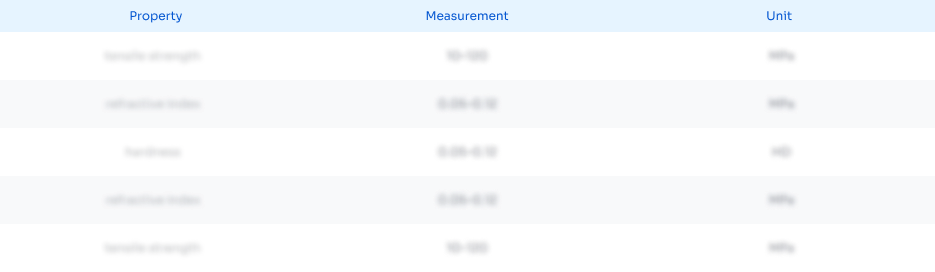
Abstract
Description
Claims
Application Information

- R&D
- Intellectual Property
- Life Sciences
- Materials
- Tech Scout
- Unparalleled Data Quality
- Higher Quality Content
- 60% Fewer Hallucinations
Browse by: Latest US Patents, China's latest patents, Technical Efficacy Thesaurus, Application Domain, Technology Topic, Popular Technical Reports.
© 2025 PatSnap. All rights reserved.Legal|Privacy policy|Modern Slavery Act Transparency Statement|Sitemap|About US| Contact US: help@patsnap.com