Visbreaking-coking combined process method by hydrogen generated from heavy oil
A combined process and hydrogen supply technology, which is applied in the direction of only multi-stage series refining and cracking process treatment, to achieve the effects of increasing diesel yield, strong competitiveness, and reducing hydrogen supply costs
- Summary
- Abstract
- Description
- Claims
- Application Information
AI Technical Summary
Problems solved by technology
Method used
Image
Examples
Embodiment 1
[0021] Fresh heavy oil raw material (a kind of super heavy oil, wherein the viscosity at 80°C is 1454mm 2 / s) and coking narrow fraction (350-420°C) are blended at a ratio of 0.05-0.50, and the obtained blended oil is subjected to visbreaking process. The reaction conditions are: reaction temperature 420°C, residence time 30min, reaction pressure 0.4 MPa(G), the viscosity-reduced product is separated by a fractionation tower, and the gas and gasoline fractions are separated, and the obtained viscosity-reduced residual oil is subjected to delayed coking processing. The coking reaction conditions are: reaction temperature 490 ° C, coke tower top pressure 0.18MPa(G). Results The product yields of the combined process were as follows: coke yield 11.94%, gas yield 7.42%, liquid yield 80.64%, light oil 54.10% (including diesel oil 32.26%).
Embodiment 2
[0025] Fresh heavy oil raw material (a kind of super heavy oil, wherein the viscosity at 80°C is 1454mm 2 / s) and coking narrow fraction (240-350°C) are blended at a ratio of 0.05-0.50, and the obtained blended oil is subjected to visbreaking process. The reaction conditions are: reaction temperature 420°C, residence time 30min, reaction pressure 0.4 MPa(G), the viscosity-reduced product is separated by a fractionation tower, and the gas and gasoline fractions are separated, and the obtained viscosity-reduced residual oil is subjected to delayed coking processing. The coking reaction conditions are: reaction temperature 490 ° C, coke tower top pressure 0.18MPa(G). Results The combined process yields were as follows: coke yield 12.44%, gas yield 7.46%, liquid yield 80.10%, light oil 55.65% (including diesel oil 32.49%).
[0026] Comparative Example 1: The fresh raw material of heavy oil is directly processed according to the conditions of delayed coking in Example 1, and the p...
PUM
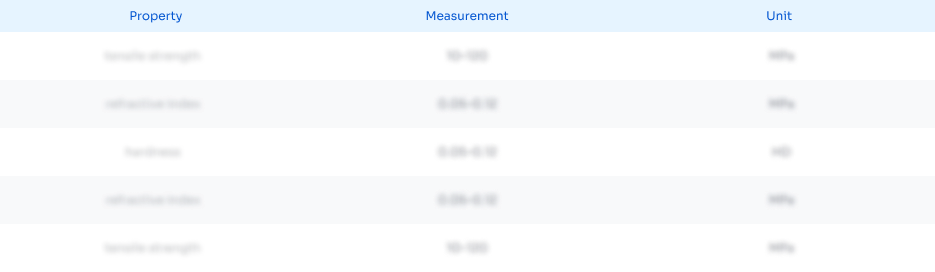
Abstract
Description
Claims
Application Information

- R&D Engineer
- R&D Manager
- IP Professional
- Industry Leading Data Capabilities
- Powerful AI technology
- Patent DNA Extraction
Browse by: Latest US Patents, China's latest patents, Technical Efficacy Thesaurus, Application Domain, Technology Topic, Popular Technical Reports.
© 2024 PatSnap. All rights reserved.Legal|Privacy policy|Modern Slavery Act Transparency Statement|Sitemap|About US| Contact US: help@patsnap.com