Light diffusing element, polarizing plate with light diffusing element, liquid crystal display using both, and manufacturing method for light diffusing element
A manufacturing method and light diffusion technology, which are applied to semiconductor devices of light-emitting elements, optical elements, and parts of lighting devices, etc., can solve the problems of complex manufacturing process, insufficient productivity, and impractical use of fine particles, and achieve the goal of suppressing backlash. Scattering, cost-effective, and the effect of widening the difference in refractive index
- Summary
- Abstract
- Description
- Claims
- Application Information
AI Technical Summary
Problems solved by technology
Method used
Image
Examples
Embodiment 1
[0144]
[0145] To 18.2 parts of hard coat resin (manufactured by JSR Corporation, trade name "Opstar KZ6661" (containing MEK / MIBK) was added 6.8 parts of 50% methyl ethyl ketone (MEK ) solution, 0.068 parts of photopolymerization initiator (manufactured by Ciba Specialty Chemicals, trade name "Irgacure 907"), 0.625 parts of leveling agent (manufactured by DIC Corporation, trade name "GRANDIC PC 4100"), and 2.5 parts of polymethyl methacrylate (PMMA) fine particles (manufactured by Soken Chemical Co., Ltd., trade name "MX 180 TA", average particle diameter 1.8 μm, refractive index 1.49) as light diffusing fine particles. The mixture was ultrasonically processed for 5 minutes to prepare a coating solution that was uniformly dispersed with the above-mentioned components. The solid content of the coating solution was 54.5%. After preparing the coating solution, the coating solution was immediately coated with a rod machine-coated on a TAC film (manufactured by Fuji Photo Film...
Embodiment 2
[0147]
[0148] Except having changed the coating thickness of the coating liquid, it carried out similarly to Example 1, and obtained the light-diffusion element of thickness 16 micrometers. The obtained light-diffusing element was used for the evaluation of said (1)-(6). The results are shown in Table 1.
Embodiment 3
[0149]
[0150] Except having changed the coating thickness of the coating liquid, it carried out similarly to Example 1, and obtained the light-diffusion element of thickness 4 micrometers. The obtained light-diffusing element was used for the evaluation of said (1)-(6). The results are shown in Table 1.
PUM
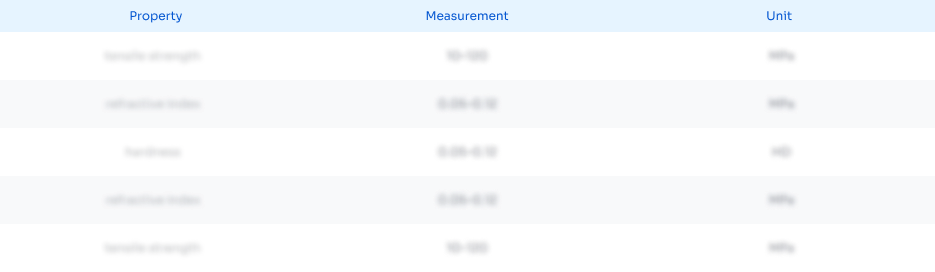
Abstract
Description
Claims
Application Information

- R&D
- Intellectual Property
- Life Sciences
- Materials
- Tech Scout
- Unparalleled Data Quality
- Higher Quality Content
- 60% Fewer Hallucinations
Browse by: Latest US Patents, China's latest patents, Technical Efficacy Thesaurus, Application Domain, Technology Topic, Popular Technical Reports.
© 2025 PatSnap. All rights reserved.Legal|Privacy policy|Modern Slavery Act Transparency Statement|Sitemap|About US| Contact US: help@patsnap.com