Slide bearing component, slide bearing and method of manufacturing slide bearing component
A sliding bearing and component technology, applied in bearing components, shafts and bearings, mechanical equipment, etc., can solve the problems of plastic damage to sliding materials, glass fiber wear, damage to mating surfaces, etc., and achieve good sliding characteristics and long service life. Effect
- Summary
- Abstract
- Description
- Claims
- Application Information
AI Technical Summary
Problems solved by technology
Method used
Image
Examples
Embodiment Construction
[0024] figure 1 A schematic sectional view of an exemplary embodiment of a plain bearing designed according to the invention is shown. The plain bearing is designed as a radial bearing and has an outer ring 1 and an inner ring 2 each having a cylindrical design. The outer ring 1 has a cylindrical sliding pad 3 which is fixedly connected to a cylindrical bearing structure 4 . In the exemplary embodiment shown, the sliding pad 3 is designed as a coating which is applied to the support structure 4 , for example in an injection molding process. However, it is also possible for the sliding pad 3 to be designed as a separate component and to be glued or screwed to the support structure 4 or fastened to the support structure 4 in some other way. Furthermore, it is possible for the sliding pad 3 and the bearing structure 4 to be formed in one piece and to consist of the same material. The inner peripheral surface of the sliding pad 3 is designed as a sliding surface 5 .
[0025] T...
PUM
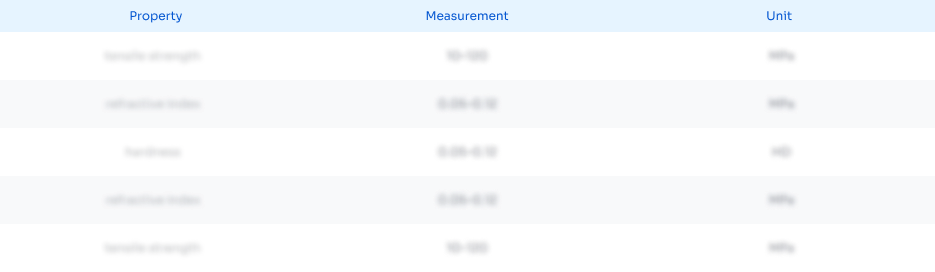
Abstract
Description
Claims
Application Information

- R&D Engineer
- R&D Manager
- IP Professional
- Industry Leading Data Capabilities
- Powerful AI technology
- Patent DNA Extraction
Browse by: Latest US Patents, China's latest patents, Technical Efficacy Thesaurus, Application Domain, Technology Topic, Popular Technical Reports.
© 2024 PatSnap. All rights reserved.Legal|Privacy policy|Modern Slavery Act Transparency Statement|Sitemap|About US| Contact US: help@patsnap.com