Processing technique of 2,6-ditbutyl-4-methylphenol
A technology of methyl phenol and di-tert-butyl, which is applied in the production process field of 2.6-di-tert-butyl-4-methylphenol, and can solve the problems such as general purification effect
- Summary
- Abstract
- Description
- Claims
- Application Information
AI Technical Summary
Problems solved by technology
Method used
Image
Examples
Embodiment 1
[0028] Add 500 grams of p-cresol and 3 grams of methanesulfonic acid into a 1000ml four-necked flask equipped with a stirring tube, condenser tube, thermometer and isobutylene inlet tube. The temperature is raised to 70~72℃ under stirring, and isobutylene gas is slowly introduced to adjust The feeding speed is to ensure that there is no gas overflowing the reaction flask. After aeration time is about 8 hours, after sampling and detecting that the content of p-cresol is less than 5%, stop the aeration and keep it at this temperature for 2 hours to complete the alkylation reaction. 92.7% crude 2.6-di-tert-butyl-4-methylphenol. Then lower the temperature to below 30°C, slowly add 30% sodium hydroxide solution, adjust the pH to 7, add 500ml of water, stir for 2 hours, stand still, separate the water layer, introduce the organic phase into the rectifying flask, and reduce Pressure distillation, collect 988 grams of 158~162°C / 5mmHg fraction, add this fraction to a 2000ml reaction fla...
Embodiment 2
[0030] Add 500 grams of p-cresol and 6 grams of methanesulfonic acid to a 1000ml four-necked flask with a stirring tube, condenser tube, thermometer and isobutylene inlet tube. The temperature is raised to 78~80℃ under stirring, and isobutylene gas is slowly introduced to adjust The feeding speed is to ensure that there is no gas overflowing the reaction flask. After the aeration time is about 8 hours, after sampling and detecting that the p-cresol content is less than 5%, stop the aeration and keep it at this temperature for 2 hours. The alkylation reaction yield is 94.5. % Crude product of 2.6-di-tert-butyl-4-methylphenol. Then lower the temperature to below 30°C, slowly add 30% sodium hydroxide solution, adjust the pH to 7, add 800ml of water, stir for 2 hours, stand still, separate the water layer, introduce the organic phase into the distillation flask, and reduce Pressure distillation, collect 995 grams of 158~162℃ / 5mmHg fraction, add this fraction to a 2000ml reaction fl...
Embodiment 3
[0032] Add 500 grams of p-cresol and 3 grams of sulfamic acid into a 1000ml four-necked flask equipped with a stirring tube, condenser tube, thermometer and isobutylene inlet tube. The temperature is raised to 70-72°C while stirring, and isobutylene gas is slowly introduced. Enter the speed to ensure that there is no gas overflowing the reaction flask. After aeration time is about 8 hours, after sampling and detecting that the content of p-cresol is less than 5%, stop the aeration and keep it at this temperature for 2 hours. The alkylation reaction yield is 93.8%. The crude product of 2.6-di-tert-butyl-4-methylphenol. Then lower the temperature to below 30°C, slowly add 30% sodium hydroxide solution, adjust the pH to 7, add 500ml of water, stir for 2 hours, stand still, separate the water layer, introduce the organic phase into the rectifying flask, and reduce Pressure distillation, collect 990 grams of 158~162°C / 5mmHg fraction, add this fraction to a 2000ml reaction flask, add...
PUM
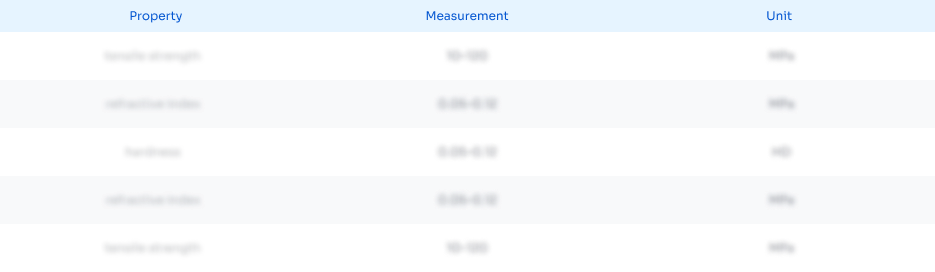
Abstract
Description
Claims
Application Information

- Generate Ideas
- Intellectual Property
- Life Sciences
- Materials
- Tech Scout
- Unparalleled Data Quality
- Higher Quality Content
- 60% Fewer Hallucinations
Browse by: Latest US Patents, China's latest patents, Technical Efficacy Thesaurus, Application Domain, Technology Topic, Popular Technical Reports.
© 2025 PatSnap. All rights reserved.Legal|Privacy policy|Modern Slavery Act Transparency Statement|Sitemap|About US| Contact US: help@patsnap.com