Oil distribution device for rolling mill
A technology of oil distribution and rolling mill, applied in the direction of roll, metal rolling, metal rolling, etc., can solve the problems of surface alloy plate pull loss, waste of lubricating oil, large production noise, etc., to improve the efficiency of finished products and improve the uniformity of oil coating degree of effect
- Summary
- Abstract
- Description
- Claims
- Application Information
AI Technical Summary
Problems solved by technology
Method used
Image
Examples
Embodiment Construction
[0011] The specific implementation manners of the present invention will be described in further detail below in conjunction with the accompanying drawings, so as to make the technical solution of the present invention easier to understand and grasp.
[0012] The invention improves the oil distribution device of the upper pressing roll aiming at the defects in the actual application process of the special rolling mill for bimetallic compounding. Specifically: if figure 1 As shown, the oil distribution device 2 is integrally integrated on the upper pressure roller 1, the first side of the oil distribution device 2 facing away from the upper pressure roller is provided with an oil injection hole 21, and the second side close to the upper pressure roller is provided with a uniform Oil outlet holes 22 are densely distributed, and the oil outlet holes communicate with the oil injection holes in the oil distribution device body. In order to further improve the above technical solut...
PUM
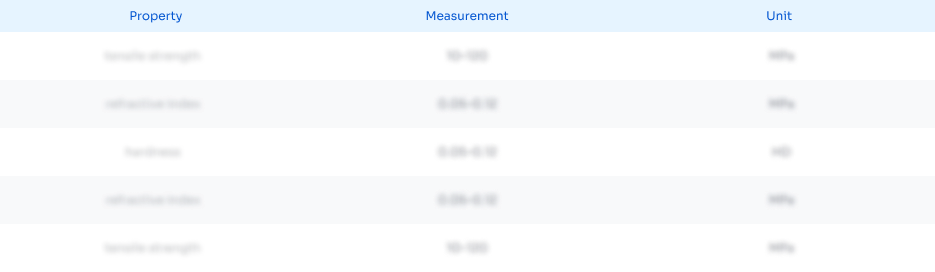
Abstract
Description
Claims
Application Information

- R&D
- Intellectual Property
- Life Sciences
- Materials
- Tech Scout
- Unparalleled Data Quality
- Higher Quality Content
- 60% Fewer Hallucinations
Browse by: Latest US Patents, China's latest patents, Technical Efficacy Thesaurus, Application Domain, Technology Topic, Popular Technical Reports.
© 2025 PatSnap. All rights reserved.Legal|Privacy policy|Modern Slavery Act Transparency Statement|Sitemap|About US| Contact US: help@patsnap.com