Spinning method
A processing method and technology to be processed, applied in the direction of engine components, mechanical equipment, etc., can solve the problems of impossible reuse of foamed resin, difficult to take out foamed resin, low productivity, etc., to prevent wrinkles, improve processing speed, and restrain elastic deformation. Effect
- Summary
- Abstract
- Description
- Claims
- Application Information
AI Technical Summary
Problems solved by technology
Method used
Image
Examples
Embodiment
[0046] As a sample, a ferritic stainless steel electric welded steel pipe with an outer diameter of 150 mm was used. At this time, three types of steel pipes with blank plate thicknesses of 0.8 mm, 1.05 mm, and 1.2 mm were used.
[0047] As the core member, a cold rolled steel sheet for spring (JISG4802, S55C-CSPB) with a thickness of 0.5 mm as a blank, a winding body having a diameter of 150 mm and a width of 100 mm is used.
[0048] Insert the above spring steel plate winding body into the pipe ends of the above three types of processed steel pipes, and the processing roller rotates at a speed of 600 rpm while contacting the processed steel pipe, and at a feed speed of 6000 mm / min, 11 passes at 60% The diameter reduction ratio (diameter reduction ratio) is reduced until the outer diameter of the tube end is 90mm.
[0049] When the thickness of the blank steel pipe is 0.8mm, even if the core member is used or not, wrinkles will occur before the diameter is reduced to 60% of the dia...
PUM
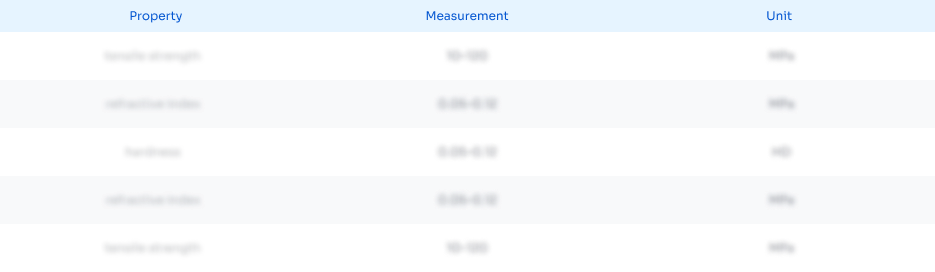
Abstract
Description
Claims
Application Information

- Generate Ideas
- Intellectual Property
- Life Sciences
- Materials
- Tech Scout
- Unparalleled Data Quality
- Higher Quality Content
- 60% Fewer Hallucinations
Browse by: Latest US Patents, China's latest patents, Technical Efficacy Thesaurus, Application Domain, Technology Topic, Popular Technical Reports.
© 2025 PatSnap. All rights reserved.Legal|Privacy policy|Modern Slavery Act Transparency Statement|Sitemap|About US| Contact US: help@patsnap.com