Method for producing synthetic ammonia and methanol raw material gas by fixed-bed intermittent oxygen-increasing natural gasification
A technology for producing synthetic ammonia and a fixed bed, which is applied in the manufacture of combustible gas, petroleum industry, etc., can solve the problems of large heat loss, low environmental pollution, and high methane content, and achieve the effects of easy adjustment and reduced operation difficulty.
- Summary
- Abstract
- Description
- Claims
- Application Information
AI Technical Summary
Problems solved by technology
Method used
Image
Examples
Embodiment Construction
[0046] To further illustrate the present invention, it will be specifically described in conjunction with the following embodiments:
[0047] A fixed-bed intermittent oxygen-enhanced natural gasification method for producing synthetic ammonia and methanol feed gas is based on the traditional fixed-bed intermittent gasification process, which improves the blowing efficiency and shortens the blowing stage by increasing the oxygen concentration in the furnace air time. When the oxygen concentration reaches a certain level, the time of the blowing stage is zero. At this time, the two stages of blowing and air purging in the fixed-bed intermittent gasification process are combined into the recovery stage of the intermittent oxygen-enriching autothermal gasification process. The process flow is as follows: (see Figure 4 ) One cycle of the fixed-bed intermittent oxygen-enhancing natural gasification process is divided into four stages: recovery, upward blowing, downward blowing, and s...
PUM
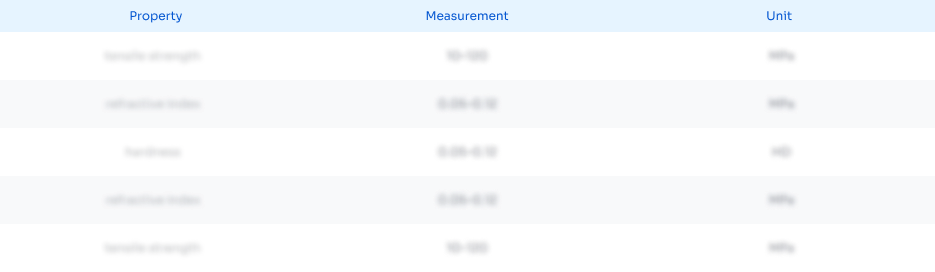
Abstract
Description
Claims
Application Information

- R&D
- Intellectual Property
- Life Sciences
- Materials
- Tech Scout
- Unparalleled Data Quality
- Higher Quality Content
- 60% Fewer Hallucinations
Browse by: Latest US Patents, China's latest patents, Technical Efficacy Thesaurus, Application Domain, Technology Topic, Popular Technical Reports.
© 2025 PatSnap. All rights reserved.Legal|Privacy policy|Modern Slavery Act Transparency Statement|Sitemap|About US| Contact US: help@patsnap.com