Pressing film method of flexible printed circuit
A flexible circuit board and film lamination technology, which is applied in printed circuit, printed circuit manufacturing, electrical components, etc., can solve problems such as poor product function, achieve the effect of eliminating air bubbles and improving the authenticity rate
- Summary
- Abstract
- Description
- Claims
- Application Information
AI Technical Summary
Problems solved by technology
Method used
Image
Examples
Embodiment Construction
[0007] Such as figure 1 As shown, the method steps of the present invention are as follows: first, apply a thin layer of water layer 4 on the material 3 to be laminated with a damp cloth, and then send it to the lamination device for lamination. The lamination temperature is 95±5°C. The laminating speed is 1.5m / min, the pressure is about 20Psi, and the upper and lower rollers 2 press the photosensitive film 1 onto the material. Because there is a thin layer of water on the surface of the material before the film is pressed, this layer of water just fills up the unevenness of the surface of the material. After the film is pressed, there will be no more air bubbles between the material and the film. The photosensitive film will absorb the water, and then the film will be tightly attached to the material, so that the line will not be broken after the laminated material is made, so the yield rate of the product will be greatly improved.
PUM
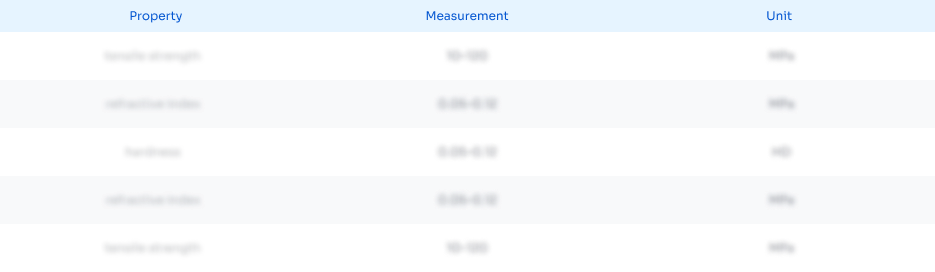
Abstract
Description
Claims
Application Information

- R&D
- Intellectual Property
- Life Sciences
- Materials
- Tech Scout
- Unparalleled Data Quality
- Higher Quality Content
- 60% Fewer Hallucinations
Browse by: Latest US Patents, China's latest patents, Technical Efficacy Thesaurus, Application Domain, Technology Topic, Popular Technical Reports.
© 2025 PatSnap. All rights reserved.Legal|Privacy policy|Modern Slavery Act Transparency Statement|Sitemap|About US| Contact US: help@patsnap.com