Lining structure of rotary kiln
A rotary kiln and lining technology, applied in the field of rotary kiln, can solve the problems of low structural strength of lightweight parts, high thermal conductivity, easy separation and falling off, etc. The effect of emissions
- Summary
- Abstract
- Description
- Claims
- Application Information
AI Technical Summary
Problems solved by technology
Method used
Image
Examples
Embodiment 1
[0046] Such as figure 1 As shown, the cement rotary kiln lining with good energy-saving effect is composed of the following materials:
[0047] Rear kiln mouth 7: composite of corundum hollow sphere lightweight castable and mullite amorphous castable;
[0048] Preheating zone 6: Alkali-resistant composite brick;
[0049] Decomposition zone 5: high alumina composite brick;
[0050] Upper transition zone 4: periclase spinel composite brick;
[0051] Firing zone 3: magnesia-chrome composite brick;
[0052] Lower transition zone 2: Silica composite brick;
[0053] Front kiln mouth 1: composite of corundum hollow sphere lightweight castable and mullite amorphous castable.
[0054] The thickness of the composite brick is 200mm, the thickness ratio of the working layer and the heat insulation layer is 1:1, and the density of the light heat insulation layer is 1.36g / cm 3 , t(°C), taking the cement rotary kiln with output of 5000t / d (Φ4.8m×72m) as an example, the refractory brick...
Embodiment 2
[0056] Such as figure 1 , the cement rotary kiln lining with good energy-saving effect is composed of the following materials:
[0057] Rear kiln mouth 7: composite of corundum hollow sphere lightweight castable and steel fiber toughened high-alumina amorphous castable;
[0058] Preheating zone 6: clay composite brick;
[0059] Decomposition zone 5: Silica composite brick;
[0060] Upper transition zone 4: periclase spinel composite brick;
[0061] Firing zone 3: periclase spinel composite brick;
[0062] Lower transition zone 2: spinel composite brick;
[0063] Front kiln mouth 1: composite of corundum hollow sphere lightweight castable and steel fiber toughened high-alumina amorphous castable.
[0064] The thickness of the composite brick is 200mm, the thickness ratio of the working layer and the heat insulation layer is 1:1, and the density of the light heat insulation layer is 1.51g / cm 3 , t(°C), taking the cement rotary kiln with output of 5000t / d (Φ4.8m×72m) as a...
Embodiment 3
[0066] Such as figure 1 As shown, the cement rotary kiln lining with good energy-saving effect is composed of the following materials:
[0067] Rear kiln mouth 7: steel fiber reinforced high aluminum castable;
[0068] Preheating zone 6: Alkali-resistant castable;
[0069] Decomposition zone 5: Silica composite brick;
[0070] Upper transition zone 4: magnesium-calcium composite brick;
[0071] Firing zone 3: Magnesium-calcium-zirconium composite brick;
[0072] Lower transition zone 2: Silica composite brick;
[0073] Front kiln mouth 1: steel fiber reinforced high alumina castable.
PUM
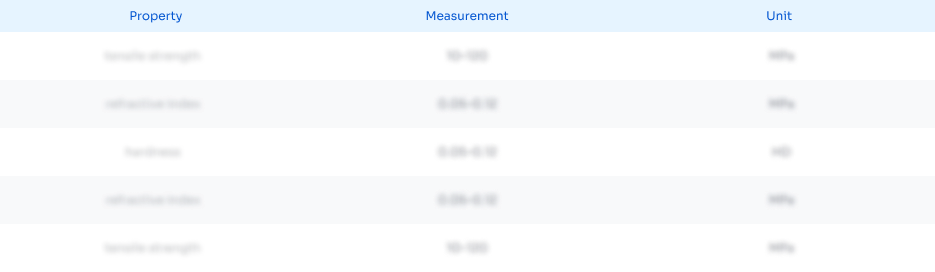
Abstract
Description
Claims
Application Information

- Generate Ideas
- Intellectual Property
- Life Sciences
- Materials
- Tech Scout
- Unparalleled Data Quality
- Higher Quality Content
- 60% Fewer Hallucinations
Browse by: Latest US Patents, China's latest patents, Technical Efficacy Thesaurus, Application Domain, Technology Topic, Popular Technical Reports.
© 2025 PatSnap. All rights reserved.Legal|Privacy policy|Modern Slavery Act Transparency Statement|Sitemap|About US| Contact US: help@patsnap.com