Method for operating electric motor
A technology of electric motor and back electromotive force, applied in the direction of AC motor control, electronic commutation motor control, electrical components, etc., can solve the problems of motor power and efficiency reduction, inaccuracy, sound interference, etc., and achieve reduced deviation and high efficiency , The effect of uniform motor operation
- Summary
- Abstract
- Description
- Claims
- Application Information
AI Technical Summary
Problems solved by technology
Method used
Image
Examples
Embodiment Construction
[0029] In the method for operating an electric motor, as electric motor 1, provided in figure 1 The brushless DC motor shown only schematically in the form of an equivalent circuit diagram. The electric motor 1 has a primary part and a secondary part which is mounted rotatably relative to the primary part about an axis of rotation. The primary part is designed as a stator and the secondary part is designed as a rotor. The electric motor can also be a linear motor.
[0030]The primary part has a polyphase field coil with three windings 2 a , 2 b , 2 c which are each connected at one end to the neutral point 3 and at the other end to the current flowing from the electric motor 1 . The phase terminals 4a, 4b, 4c are connected. Each phase terminal 4a, 4b, 4c is respectively connected to an output terminal 5a, 5b, 5c of an output stage 6, which is only partially shown in the figure. The secondary part has permanently magnetic poles which are spaced apart from one another in the...
PUM
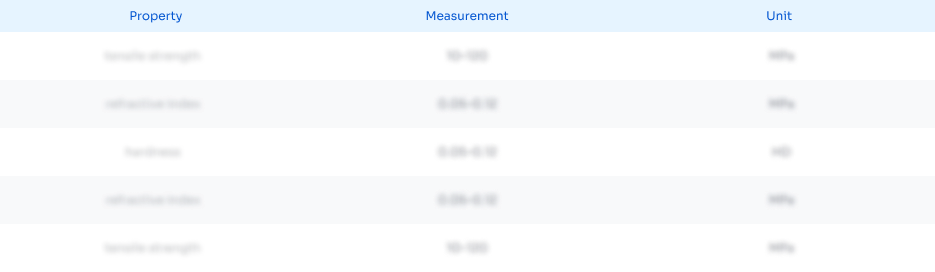
Abstract
Description
Claims
Application Information

- R&D
- Intellectual Property
- Life Sciences
- Materials
- Tech Scout
- Unparalleled Data Quality
- Higher Quality Content
- 60% Fewer Hallucinations
Browse by: Latest US Patents, China's latest patents, Technical Efficacy Thesaurus, Application Domain, Technology Topic, Popular Technical Reports.
© 2025 PatSnap. All rights reserved.Legal|Privacy policy|Modern Slavery Act Transparency Statement|Sitemap|About US| Contact US: help@patsnap.com