Two-stage rotary mechanism for small electric manipulator
An electric manipulator and rotary mechanism technology, applied in manipulators, manufacturing tools, joints, etc., can solve problems such as unfavorable miniaturization and complex structure, and achieve the effect of being conducive to miniaturization, compact structure and convenient control
- Summary
- Abstract
- Description
- Claims
- Application Information
AI Technical Summary
Problems solved by technology
Method used
Image
Examples
Embodiment Construction
[0022] The present invention will be described in more detail below with reference to the accompanying drawings.
[0023] combine figure 1 , figure 2 , the main components of the present invention include the manipulator shell 15, the wrist joint drive motor 22, the claw drive motor 16, the wrist joint shell 6, the watertight cable socket 25, the manipulator shell cover 29, and the first stage rotary mechanism and the second stage The main structural components such as the slewing mechanism, the first-stage slewing mechanism includes the claw motor housing 14, the first-stage sliding bearing 13 and the first-stage gray ring 9, the second-stage slewing mechanism includes the claw drive shaft 1, the second-stage sliding Bearing 4 and second stage gray circle 5.
[0024] Wherein the wrist joint drive motor 22 is fixed with the wrist joint motor connection plate 20 through the wrist joint motor screw 21, the wrist joint motor connection plate 20 is fixed with the mechanical arm...
PUM
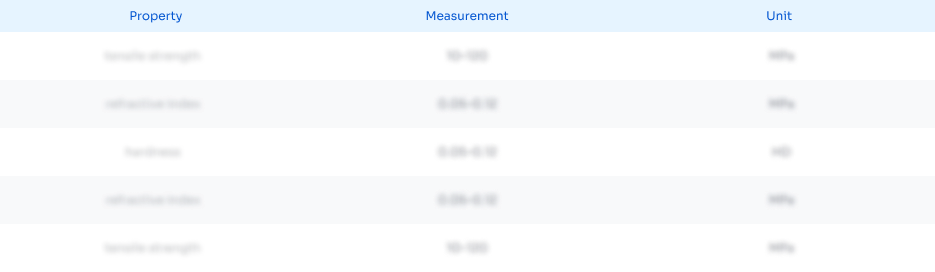
Abstract
Description
Claims
Application Information

- R&D Engineer
- R&D Manager
- IP Professional
- Industry Leading Data Capabilities
- Powerful AI technology
- Patent DNA Extraction
Browse by: Latest US Patents, China's latest patents, Technical Efficacy Thesaurus, Application Domain, Technology Topic, Popular Technical Reports.
© 2024 PatSnap. All rights reserved.Legal|Privacy policy|Modern Slavery Act Transparency Statement|Sitemap|About US| Contact US: help@patsnap.com