Casting technology for gyroscope motor rotor
A technology of motor rotor and casting process, which is used in the manufacture of motor generators, stator/rotor bodies, electrical components, etc., can solve the problems of low yield, uneven organization, hidden dangers, etc., to improve productivity and ensure stable quality the effect of eliminating security risks
- Summary
- Abstract
- Description
- Claims
- Application Information
AI Technical Summary
Problems solved by technology
Method used
Examples
Embodiment Construction
[0010] A kind of gyroscope motor rotor casting process of the present invention, use equipment is 14OT cold chamber die-casting machine, accumulator is piston type, and accumulator pressure is placed on 12-15MPa, and the specific technological process of this invention is:
[0011] 1. Debug the die-casting machine and die-casting mold, the system pressure of the die-casting machine is 130T;
[0012] 2. The crucible is preheated at a temperature of 150-200°C, the aluminum ingot is smelted and purified at a temperature of 720-760°C, and the temperature is lowered to 700°C after refining;
[0013] 3. Die-casting mold pressure test 30-50 molds, make the mold temperature reach 220-250 ℃, clean the cavity and runner, and insert the rotor laminations in the oven to preheat to 75-80 ℃;
[0014] 4. Die-casting molding: Spray release agent in the cavity → mold closing → mold closing delay → injection → pressure holding delay → primary parting, punch and material handle separation → seco...
PUM
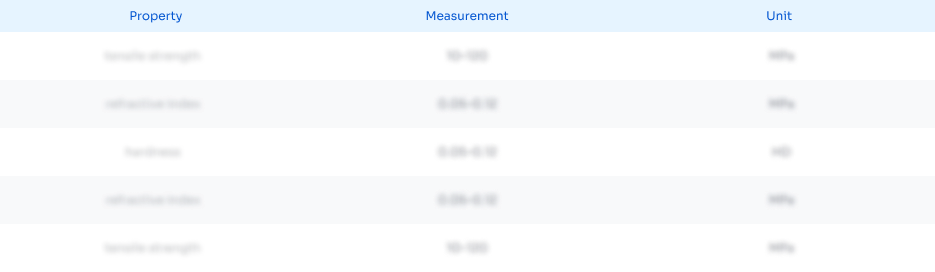
Abstract
Description
Claims
Application Information

- R&D Engineer
- R&D Manager
- IP Professional
- Industry Leading Data Capabilities
- Powerful AI technology
- Patent DNA Extraction
Browse by: Latest US Patents, China's latest patents, Technical Efficacy Thesaurus, Application Domain, Technology Topic, Popular Technical Reports.
© 2024 PatSnap. All rights reserved.Legal|Privacy policy|Modern Slavery Act Transparency Statement|Sitemap|About US| Contact US: help@patsnap.com