Micro-foaming injection-molded screw
An injection molding and micro-foaming technology, applied in the field of injection molding screw, can solve problems such as insufficient mixing and homogenization ability, and achieve the effects of increasing mixing and homogenizing ability, stable pressure and speed, and avoiding the countercurrent flow of the melt to block the air passage.
- Summary
- Abstract
- Description
- Claims
- Application Information
AI Technical Summary
Problems solved by technology
Method used
Image
Examples
Embodiment Construction
[0017] like figure 1 As shown, a micro-foaming injection molding screw mainly consists of a rear screw 1, a rear positioning ring 2, a rear check ring 3, a rear mixing section 4, a front mixing section 5, a front screw 6, a front positioning ring 7, The front check ring 8 and the screw head 9 are composed; the tail of the rear screw 1 has a keyway, which is installed on the injection machine through the keyway and the key; the head of the rear screw 1 has a threaded hole, and the tail of the rear mixing section 4 has a rear The stepped shaft 11, the end of the rear stepped shaft 11 has a rear stepped shaft thread 12, the rear positioning ring 2 and the rear check ring 3 are sequentially set on the rear stepped shaft 11 of the rear mixing section 4, and the rear mixing section 4 passes through The rear stepped shaft 11 is connected to the rear screw 1; the head of the rear mixing section 4 has a front stepped shaft 14, the end of the front stepped shaft 14 has a front stepped s...
PUM
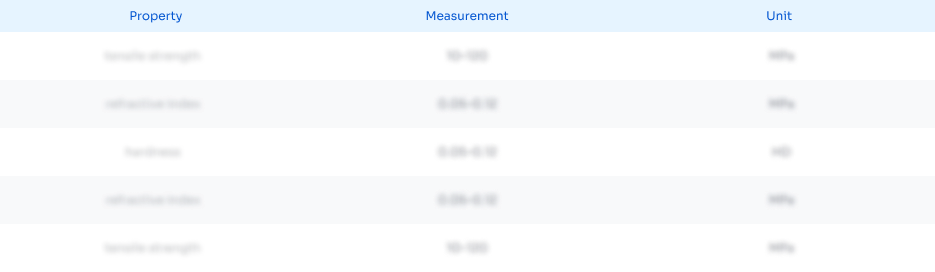
Abstract
Description
Claims
Application Information

- R&D
- Intellectual Property
- Life Sciences
- Materials
- Tech Scout
- Unparalleled Data Quality
- Higher Quality Content
- 60% Fewer Hallucinations
Browse by: Latest US Patents, China's latest patents, Technical Efficacy Thesaurus, Application Domain, Technology Topic, Popular Technical Reports.
© 2025 PatSnap. All rights reserved.Legal|Privacy policy|Modern Slavery Act Transparency Statement|Sitemap|About US| Contact US: help@patsnap.com