Oredressing method for removing sesquioxide of iron and aluminum
A technology of sesquioxide and beneficiation method, used in flotation, solid separation and other directions, can solve the problems of large mud content, loss of phosphorus minerals, and high degree of weathering, and achieve reduction in content, purification process, and impurity content. low effect
- Summary
- Abstract
- Description
- Claims
- Application Information
AI Technical Summary
Problems solved by technology
Method used
Image
Examples
Embodiment 1
[0033] Ore samples from Jinning Phosphate Mining Area, Yunnan, raw ore P 2 o 5 Content 19.74wt%, MgO content 1.31wt%, Fe 2 o 3 Content 1.68wt%, Al 2 o 3 The content is 2.69wt%. According to the above-mentioned process scheme of the present invention, phosphorus enrichment by forward and reverse flotation + reverse flotation to remove R under normal temperature conditions 2 o 3 The combined process flow to obtain phosphorous concentrate P 2 o 5 Content 30.40wt%, MgO content 0.26wt%, Fe 2 o 3 Content 0.90wt%, Al 2 o 3 Content 1.09wt%, where Fe 2 o 3 Exclusion rate: 72.51wt%, Al 2 o 3 Exclusion rate: 81.10wt%. Phosphate concentrate (Fe 2 o 3 +Al 2 o 3 +MgO)≤2.3wt%, CaO / P 2 o 5 =1.39, MgO / P 2 o 5 =0.86wt%, Fe 2 o 3 / P 2 o 5 =2.96wt%, Al 2 o 3 / P 2 o 5 =3.59wt%, MER=7.40wt% (Note: MER (impurity index) = (Fe 2 o 3 +Al 2 o 3 +MgO) / P 2 o 5 ).
Embodiment 2
[0035] Ore samples from Jinning Phosphate Mining Area, Yunnan, raw ore P 2 o 5 Content 20.03wt%, MgO content 1.13wt%, Fe 2 o 3 Content 1.73wt%, Al 2 o 3 The content is 3.21wt%. According to the above-mentioned technological scheme of the present invention, phosphorus-enriching + reverse flotation is used to remove R at room temperature. 2 o 3 The combined process flow to obtain phosphorous concentrate P 2 o 5 Content 30.96wt%, MgO content 0.60wt%, Fe 2 o 3 Content 0.81wt%, Al 2 o 3Content 0.79wt%, where Fe 2 o 3 Exclusion rate: 74.93wt%, Al 2 o 3 Exclusion rate: 82.06wt%. Phosphate concentrate (Fe 2 o 3 +Al 2 o 3 +MgO)≤2.2wt%, CaO / P 2 o 5 =1.39, MgO / P 2 o 5 =1.94wt%, Fe 2 o 3 / P 2 o 5 =2.62wt%, Al 2 o 3 / P 2 o 5 =2.55wt%, MER=7.11wt% (Note: MER (impurity index) = (Fe 2 o 3 +Al 2 o 3 +MgO) / P 2 o 5 ).
Embodiment 3
[0037] Mining sample of Kunyang Phosphate Mine in Yunnan Province, raw ore P 2 o 5 Content 23.47wt%, MgO content 4.98wt%, Fe 2 o 3 Content 1.31wt%, Al 2 o 3 The content is 1.19wt%. According to the above-mentioned technological scheme of the present invention, under normal temperature conditions, phosphorus enrichment through single reverse flotation + reverse flotation to remove R 2 o 3 The combined process flow to obtain phosphorous concentrate P 2 o 5 Content 30.66wt%, MgO content 0.55wt%, Fe 2 o 3 Content 0.81wt%, Al 2 o 3 Content 0.98wt%, where Fe 2 o 3 Exclusion rate: 51.62wt%, Al 2 o 3 Exclusion rate: 48.27wt%. Phosphate concentrate (Fe 2 o 3 +Al 2 o 3 +MgO)≤2.34wt%, CaO / P 2 o 5 =1.46, MgO / P 2 o 5 =1.79wt%, Fe 2 o 3 / P 2 o 5 =2.64wt%, Al 2 o 3 / P 2 o 5 =3.20wt%, MER=7.63wt% (Note: MER (impurity index) = (Fe 2 o 3 +Al 2 o 3 +MgO) / P 2 o 5 ).
[0038] In the 3 examples, the obtained phosphorus concentrate indicators all reached the fir...
PUM
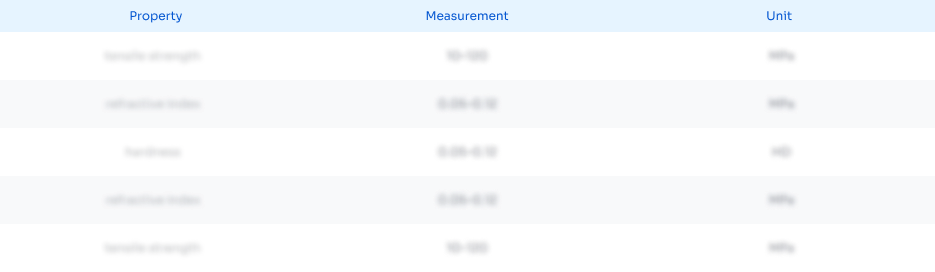
Abstract
Description
Claims
Application Information

- R&D Engineer
- R&D Manager
- IP Professional
- Industry Leading Data Capabilities
- Powerful AI technology
- Patent DNA Extraction
Browse by: Latest US Patents, China's latest patents, Technical Efficacy Thesaurus, Application Domain, Technology Topic, Popular Technical Reports.
© 2024 PatSnap. All rights reserved.Legal|Privacy policy|Modern Slavery Act Transparency Statement|Sitemap|About US| Contact US: help@patsnap.com