Method of manufacturing polymer composite member by use of two or more resins
A composite material and polymer technology, applied in the field of resin infusion technology, can solve problems such as high material cost
- Summary
- Abstract
- Description
- Claims
- Application Information
AI Technical Summary
Problems solved by technology
Method used
Image
Examples
Embodiment Construction
[0031] figure 1 A known mould arrangement 1 is shown schematically for the manufacture of fibre composite elements by using resin transfer moulding techniques. The mould arrangement 1 comprises a first mould part 2 and a second mould part 3 which are usually treated with a release agent and possibly also a coating before use. In this figure and the following figures, the first mould part 2 and the second mould part 3 are shown as rigid elements, but the second mould part 3 may also be flexible, such as by being fastened to the first mould part 3 by using a sealing tape Plastic sheet on mould part 2. A fibre layer 4, usually in the form of a mat, and possibly a release cloth (not shown) is placed on the first mould part 2, and the second mould part 3 is placed on top of it. Resin is introduced into the mould cavity 5 and into the fibers 4 via the resin inlet 6, also referred to as a resin infusion port. The preparation of the resin is not included in the figures, but is well...
PUM
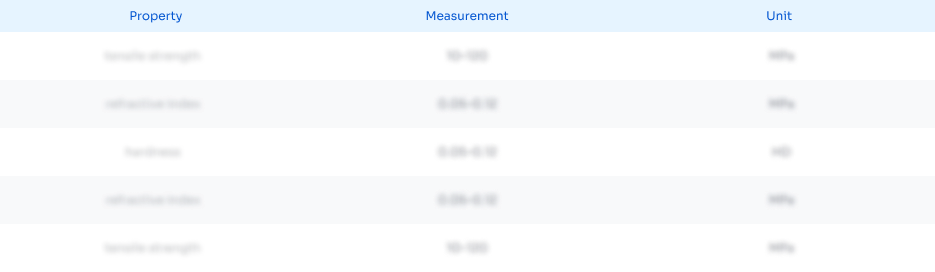
Abstract
Description
Claims
Application Information

- R&D
- Intellectual Property
- Life Sciences
- Materials
- Tech Scout
- Unparalleled Data Quality
- Higher Quality Content
- 60% Fewer Hallucinations
Browse by: Latest US Patents, China's latest patents, Technical Efficacy Thesaurus, Application Domain, Technology Topic, Popular Technical Reports.
© 2025 PatSnap. All rights reserved.Legal|Privacy policy|Modern Slavery Act Transparency Statement|Sitemap|About US| Contact US: help@patsnap.com