Ultra-high pressure fluid jetting power track transferring system and method for aircraft
A fluid jet and aircraft technology, applied in the field of aerospace vehicles, can solve the problems of consuming aircraft energy consumption, complicated design, difficult to operate, etc., and achieve the effects of low equipment cost, simple maintenance and strong penetration force.
- Summary
- Abstract
- Description
- Claims
- Application Information
AI Technical Summary
Problems solved by technology
Method used
Image
Examples
Embodiment Construction
[0081] The present invention will be described in further detail below in conjunction with the accompanying drawings, and this manufacturing technique is very clear to those skilled in the art.
[0082] The invention is applied to civil and military aviation and aerospace fields.
[0083] Effects applied to modern aircraft:
[0084] (1) When the combined nozzle holes are used as the jet parts of the empennage or ventral fin on the military or civilian aircraft with empennage, the jet effect of the honeycomb geometry arrangement
[0085] see Figure 4 : On the opposite sides of the tail of the aircraft Figure 4 -d, the plane of symmetry above and below the tail Figure 4 -e is equipped with combined nozzles, each square hole represents a nozzle with combined nozzles, after programming, it can form ever-changing forms of jetting gas.
[0086] figure 1 For example: see 1-a when the combination of nozzle holes is opened, it forms a straight jet shape; see 1-b when the combin...
PUM
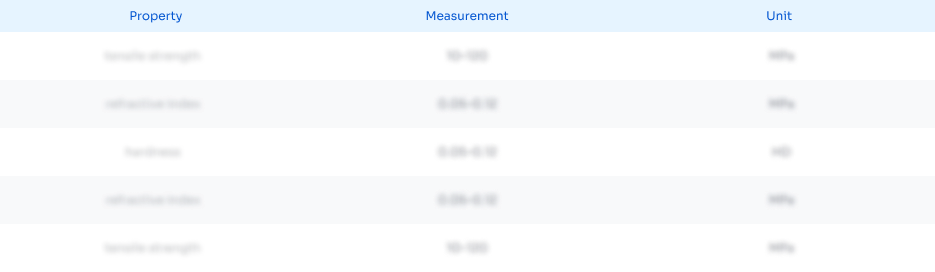
Abstract
Description
Claims
Application Information

- Generate Ideas
- Intellectual Property
- Life Sciences
- Materials
- Tech Scout
- Unparalleled Data Quality
- Higher Quality Content
- 60% Fewer Hallucinations
Browse by: Latest US Patents, China's latest patents, Technical Efficacy Thesaurus, Application Domain, Technology Topic, Popular Technical Reports.
© 2025 PatSnap. All rights reserved.Legal|Privacy policy|Modern Slavery Act Transparency Statement|Sitemap|About US| Contact US: help@patsnap.com