Crystalline silicon ingot casting method and silicon ingot
A technology for crystalline silicon and silicon ingots, applied in the field of crystalline silicon ingot casting methods and silicon ingots, can solve the problems of easy complete melting of seed crystals, unrealizable polycrystalline silicon with large grains, and poor temperature control.
- Summary
- Abstract
- Description
- Claims
- Application Information
AI Technical Summary
Problems solved by technology
Method used
Image
Examples
Embodiment Construction
[0053] The technical solutions in the embodiments of the present invention will be clarified below in conjunction with the accompanying drawings in the embodiments of the present invention
[0054]Clear and complete description, obviously, the described embodiment is only a part of the embodiment of the present invention, rather than
[0055] Full examples. Based on the embodiments of the present invention, those of ordinary skill in the art have not made any inventions
[0056] All other embodiments obtained under the premise of sexual labor all belong to the protection scope of the present invention.
[0057] In order to make the object, technical solution and advantages of the present invention clearer, the following describes the present invention with reference to the accompanying drawings:
[0058] The examples will be described in further detail.
[0059] refer to figure 1 It is a flowchart of the first embodiment of the method for casting crystalline silicon ingots...
PUM
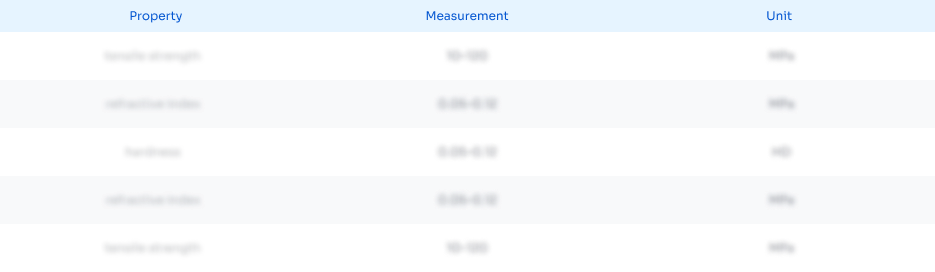
Abstract
Description
Claims
Application Information

- R&D
- Intellectual Property
- Life Sciences
- Materials
- Tech Scout
- Unparalleled Data Quality
- Higher Quality Content
- 60% Fewer Hallucinations
Browse by: Latest US Patents, China's latest patents, Technical Efficacy Thesaurus, Application Domain, Technology Topic, Popular Technical Reports.
© 2025 PatSnap. All rights reserved.Legal|Privacy policy|Modern Slavery Act Transparency Statement|Sitemap|About US| Contact US: help@patsnap.com