Coreless winding method of coiled-coil filament
A winding method and double helix technology are applied in the field of filament production of lighting bulbs, which can solve problems such as waste and environmental protection, and achieve the effects of reducing environmental protection treatment costs, reducing production processes and speeding up production speed.
- Summary
- Abstract
- Description
- Claims
- Application Information
AI Technical Summary
Problems solved by technology
Method used
Image
Examples
Embodiment Construction
[0021] see figure 1 , a coreless winding method for a double helix filament, specifically comprising the following steps:
[0022] (1) With a 500-meter-long molybdenum wire as the core wire, a 5,000-meter-long tungsten wire is wound into a spiral filament on a wire winding machine, and then sent to an annealing furnace to be heated to 1350-1400 °C, and the temperature is 3-100 °C. Surface treatment of the spiral filament at a speed of 5 m / min;
[0023] (2) Using the iron core needle as the core wire, the surface-treated helical filament and another 5,000-meter-long tungsten wire are wound into a double helical filament on a coreless wire winding machine, and then the iron core is removed. core needle, and cut the double helix filament into several sections;
[0024] (3), after the sheared double helix filament is cleaned with clear water, dry it with a drying oven;
[0025] (4) Arrange the dried double-helical filaments neatly, divide them into groups and place them in sev...
PUM
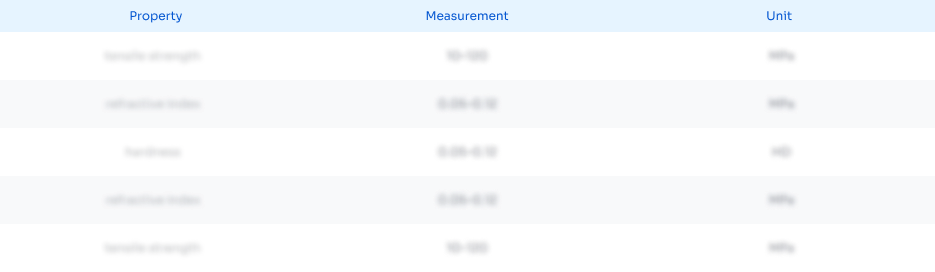
Abstract
Description
Claims
Application Information

- R&D
- Intellectual Property
- Life Sciences
- Materials
- Tech Scout
- Unparalleled Data Quality
- Higher Quality Content
- 60% Fewer Hallucinations
Browse by: Latest US Patents, China's latest patents, Technical Efficacy Thesaurus, Application Domain, Technology Topic, Popular Technical Reports.
© 2025 PatSnap. All rights reserved.Legal|Privacy policy|Modern Slavery Act Transparency Statement|Sitemap|About US| Contact US: help@patsnap.com