An aluminum alloy automatic tig no liner single-side welding double-side forming process
A single-sided welding and double-sided forming technology, applied in the field of aluminum alloy welding, can solve the problems of low welding seam pass rate, welding seam prone to cracks, workpiece deformation, etc. Beautiful effect of welding seam forming
- Summary
- Abstract
- Description
- Claims
- Application Information
AI Technical Summary
Problems solved by technology
Method used
Image
Examples
Embodiment 1
[0019] An aluminum alloy automatic TIG liner-free single-sided welding and double-sided forming process, comprising the following steps:
[0020] The first step is to select welding equipment and materials, using an automatic TIG girth welding machine, which can control the welding current, arc voltage, welding speed and wire feeding speed. Argon gas above %, the welding wire adopts ER5356Φ1.6mm welding wire, the cerium tungsten electrode Φ is 4.8mm, and the nozzle diameter of the welding torch is 19mm.
[0021] The second step is assembly and cleaning. Assembly is carried out first, assembly accuracy: misalignment ≤ 0.5mm, gap ≤ 0.5mm, and then tack welding, using MIG semi-automatic unilateral point to fix the block and cylinder, and then use acetone and stainless steel wire The wheel removes the oil and oxide film within 50mm on both sides of the groove, refer to figure 1 , 6 ~ 8mm thick aluminum alloys 1 and 2 use I-shaped groove 3, the groove angle is 50°,
[0022] The t...
Embodiment 2
[0029] An aluminum alloy automatic TIG liner-free single-sided welding and double-sided forming process, comprising the following steps:
[0030] The first step is to select welding equipment and materials, using an automatic TIG girth welding machine, which can control the welding current, arc voltage, welding speed and wire feeding speed. Argon gas above %, the welding wire adopts ER5356Φ1.6mm welding wire, the cerium tungsten electrode Φ is 4.6mm, the nozzle aperture of the welding torch is Φ18mm,
[0031] The second step is assembly and cleaning. Assembly is carried out first, assembly accuracy: misalignment ≤ 0.5mm, gap ≤ 0.5mm, and then tack welding, using MIG semi-automatic unilateral point to fix the block and cylinder, and then use acetone and stainless steel wire The wheel removes the oil and oxide film within 50mm on both sides of the groove, refer to figure 2 10-14mm thick aluminum alloys 1 and 2 use a blunt V-shaped bevel 3 with a bevel angle of 70°.
[0032] T...
PUM
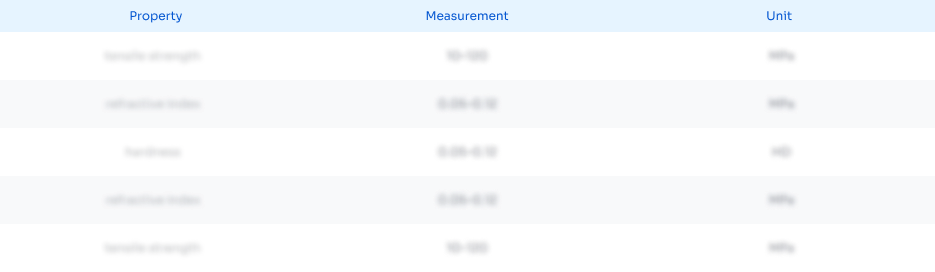
Abstract
Description
Claims
Application Information

- R&D
- Intellectual Property
- Life Sciences
- Materials
- Tech Scout
- Unparalleled Data Quality
- Higher Quality Content
- 60% Fewer Hallucinations
Browse by: Latest US Patents, China's latest patents, Technical Efficacy Thesaurus, Application Domain, Technology Topic, Popular Technical Reports.
© 2025 PatSnap. All rights reserved.Legal|Privacy policy|Modern Slavery Act Transparency Statement|Sitemap|About US| Contact US: help@patsnap.com